As an indispensable auxiliary material in fiber laser machines, compressed air has a significant impact on work efficiency and product quality during the cutting process. In the laser cutting industry, the use of compressed air to drive and cool cutting equipment and purge the cutting area are key factors to ensure cutting accuracy and efficiency. This article will explore in detail how compressed air quality affects the performance of a laser cutting machine. And this provide some suggestions for improving air quality to optimize cutting results.
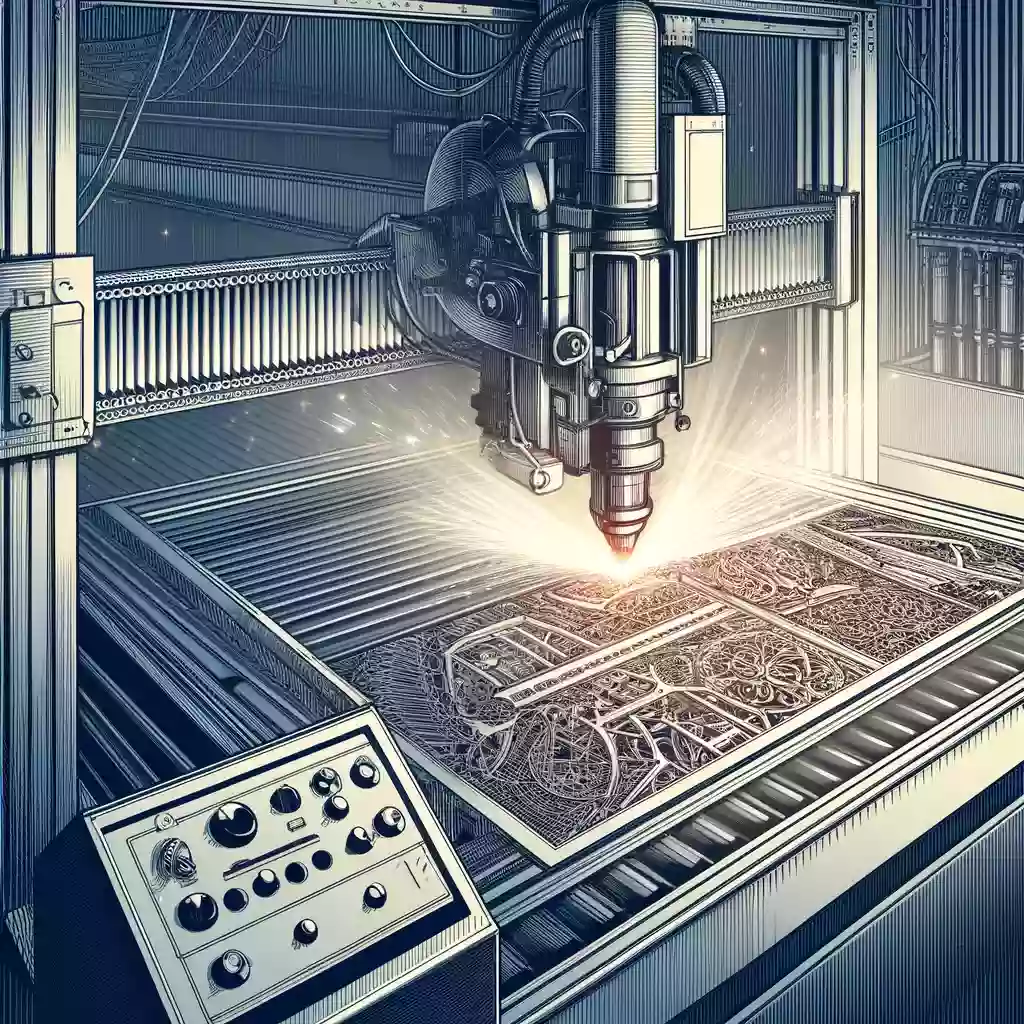
Ⅰ.The Principle of Laser Cutting
Fiber laser machine is one of the thermal cutting methods. It uses a focused high-power density laser beam to irradiate the workpiece. These causing the irradiated material to quickly melt, vaporize, ablate or reach the ignition point. At the same time, the molten material is blown away by high-speed airflow coaxial with the beam. Thereby achieving cutting of the workpiece. Laser cutting has four categories: laser vapor cutting, laser melting cutting, laser oxygen cutting and laser scribing.
Ⅱ.Advantages of Using Compressed Air Laser Cutting
Advantages: good cutting quality, narrow incision, good slit, smooth and beautiful cutting surface. These advantages can even be used as the final processing step, no need for mechanical processing, small deformation of the workpiece, high cutting accuracy, non-contact cutting, no tool wear.
Ⅲ.Disadvantages of Using Compressed Air Laser Cutting:
High cost of oxygen (02), high cost of ammonia (N2), and high gas consumption during cutting.
Ⅳ.The Importance of Compressed Air
During the laser cutting process, compressed air is mainly used to blow away the slag in the cutting area, cool the cutting parts. These help drive the operation of mechanical equipment. Proper use of compressed air can significantly increase cutting speed and cutting quality. reduce heat-affected areas, prevent oxidation of cutting surfaces, and improve the overall beauty and accuracy of the product.
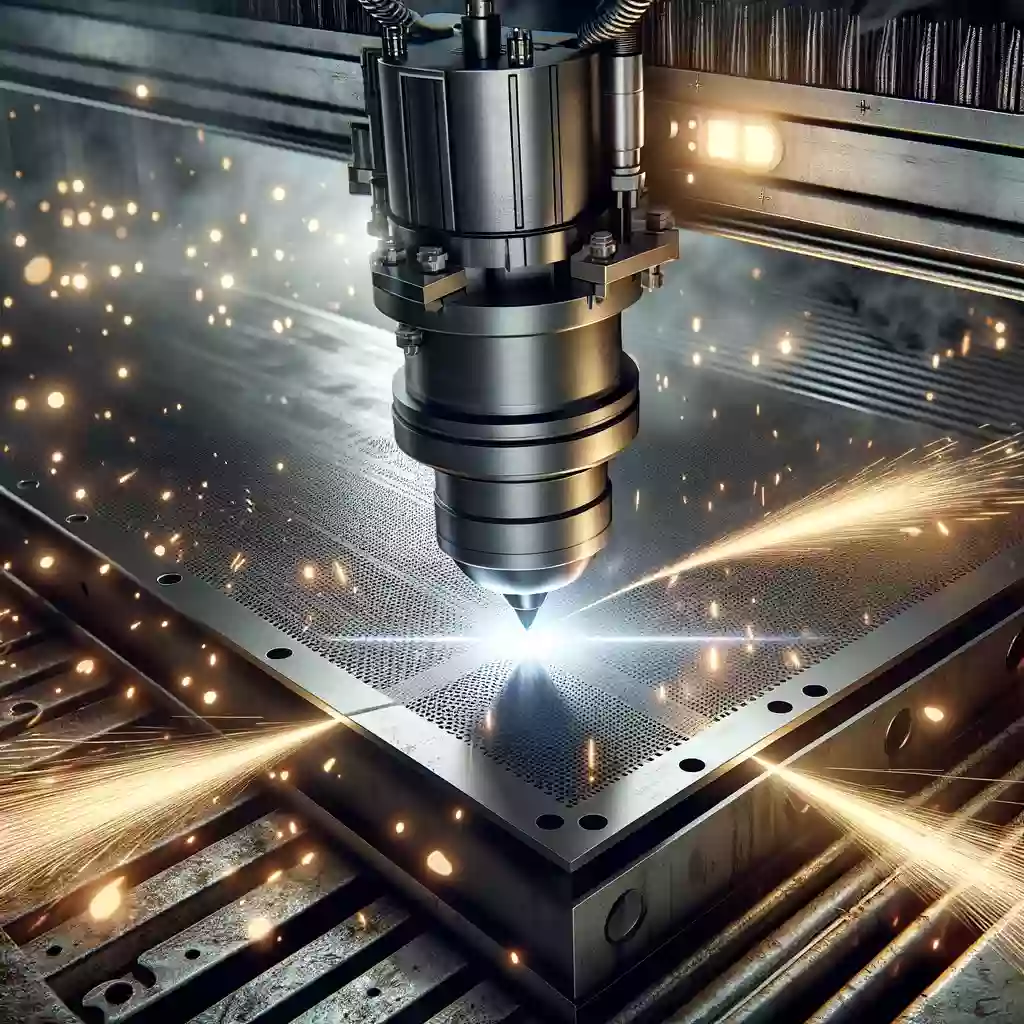
Ⅴ.Factors Affecting Compressed Air Quality
The quality of compressed air is mainly determined by the following aspects:
1.Humidity:
Moisture in compressed air can have a negative impact on the laser cutting process. Water vapor will condense under high temperature. These cause uneven oxidation or other chemical reactions on the metal surface, affecting cutting quality.
2.Oil:
The compressor may produce oil mist during operation. If this oil mist is not effectively filtered, it will form a film on the metal surface. These affect the cooling effect of the cutting parts, and may even cause damage to the cutting head.
3.Particles:
Dust and particles in the air can cause wear and clogging of the cutting head during the cutting process, reducing the quality of the laser beam and cutting accuracy.
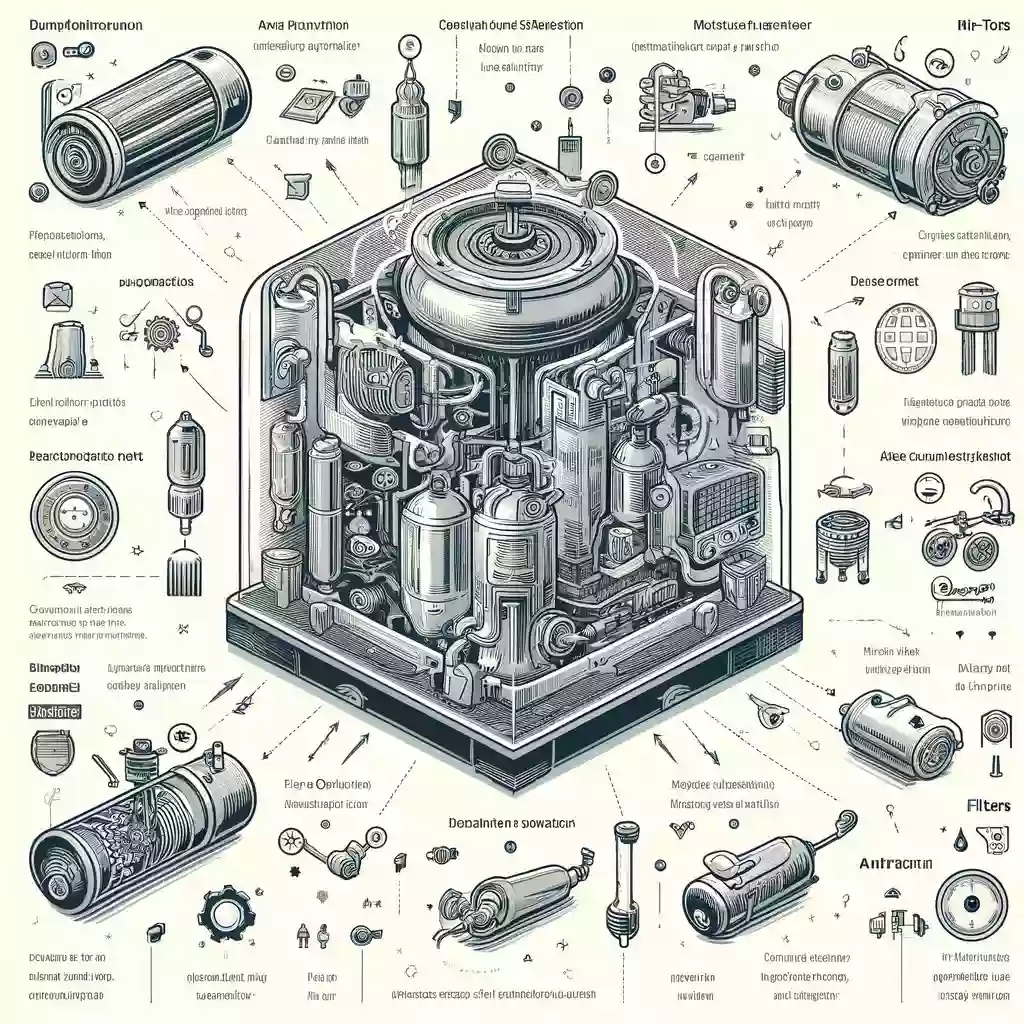
Ⅵ.Methods to Improve Compressed Air Quality
In order to ensure the efficient and precise operation of the laser cutting machine, effective measures must be taken to improve the quality of compressed air:
1.Install an efficient dryer:
Use a refrigerated or adsorption dryer to effectively remove moisture from compressed air and prevent water vapor from condensing.
2.Use high-quality filters:
Installing sophisticated filters can remove oil mist and particles from the air, protect the cutting head and maintain the clarity of the laser beam.
3.Regular maintenance and inspection:
Regularly checking the sealing and filtration effect of the compressed air system, and timely replacement of filter elements and desiccants can prevent the accumulation of pollutants and the aging of the system.
Ⅶ.Application of Compressed Air in Laser Cutting Field
Laser cutting machines can cope with the cutting requirements of various materials and complex shapes. In addition to requiring a laser that can provide high energy, auxiliary gas is an indispensable substance to complete the cutting process. There are three main auxiliary gases used for laser cutting: oxygen (O2), nitrogen (N2) and compressed air (Compressed Air).
Ⅷ.Advantages of Compressed Air Compared to Oxygen and Nitrogen
Compressed air is easier to obtain than oxygen and nitrogen, and its price is very cheap compared with oxygen and nitrogen. It is very common to use compressed air as an auxiliary gas for cutting.
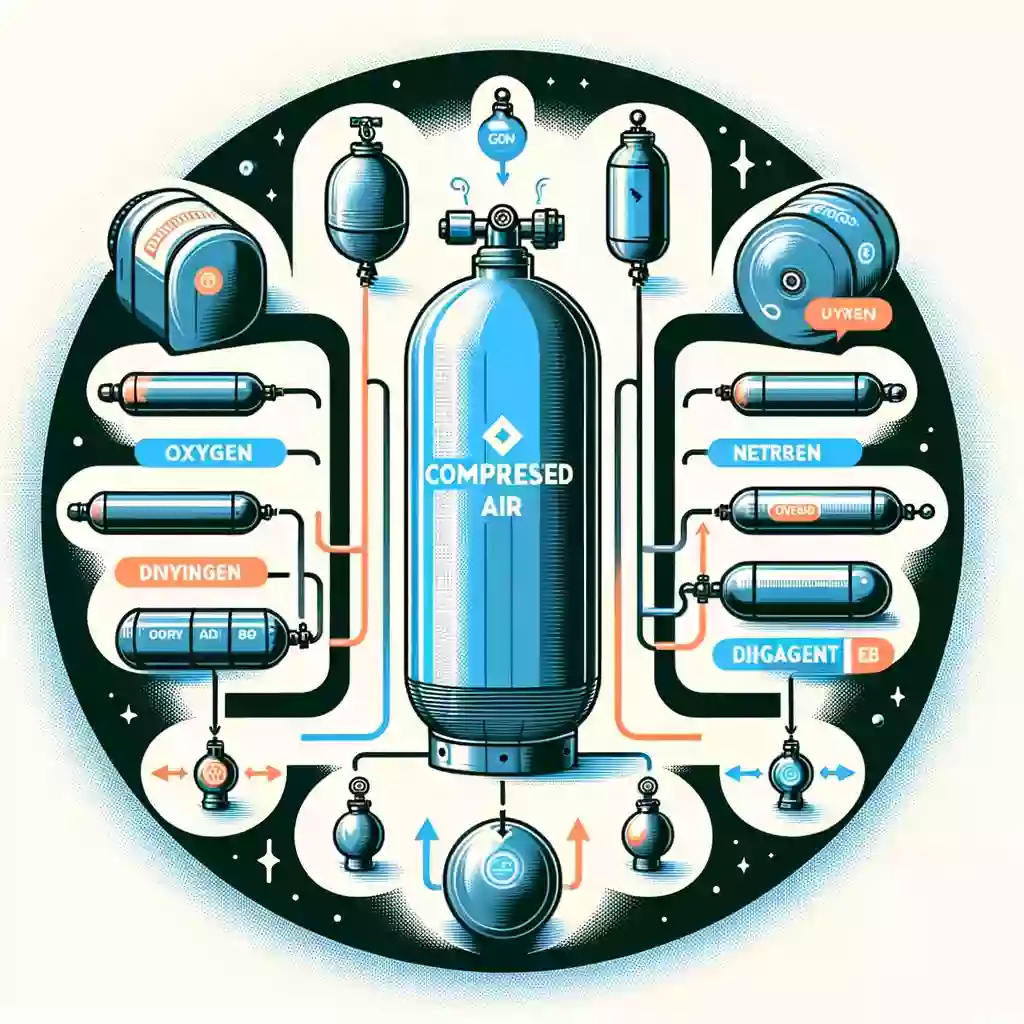
Final Thoughts
The quality of compressed air is directly related to the working efficiency and product quality of the laser cutting machine. By taking appropriate measures, such as installing efficient drying equipment and filtration systems, and performing regular maintenance and inspections, the results of laser cutting can be significantly improved. Investing in the improvement of compressed air quality will bring companies higher production efficiency and better product quality, ultimately maximizing cost-effectiveness.