Fiber laser machines are widely used in modern manufacturing due to their high efficiency, accuracy and low cost. However, as the use time increases, the cutting performance of the fiber laser cutting machine may gradually decrease, thus affecting production efficiency and product quality. To ensure consistent cutting performance from your fiber laser cutting machine, it is crucial to take appropriate precautions. This article will explore several effective methods to prevent fiber laser cutting machine cutting performance from declining.
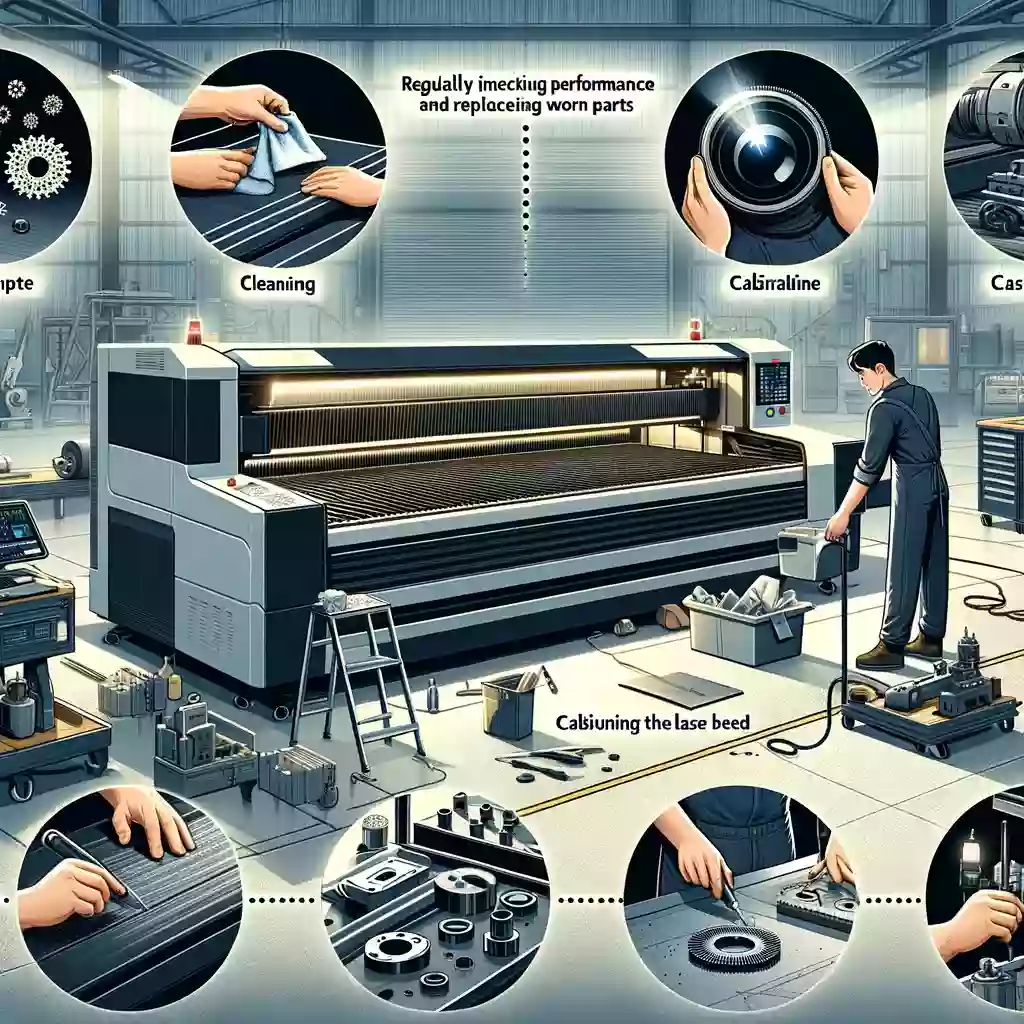
Ⅰ. Regular Maintenance and Upkeep
Regular maintenance and upkeep is one of the important measures to ensure the cutting performance of fiber laser machines. Various components of the cutting machine will wear and age during long-term operation and require regular inspection and replacement. For example, components such as fiber lasers, cutting heads, guide rails, and reflectors all need to be inspected and cleaned regularly to prevent dust and dirt from accumulating, which will affect the cutting effect.
1.Fiber laser maintenance:
Fiber laser is the core component of the cutting machine, and its performance directly affects the cutting quality. It is necessary to regularly check whether the power output of the laser is stable and clean the laser cooling system to prevent overheating.
2.Maintenance of cutting head:
The cutting head includes nozzles and lenses, which need to be cleaned and replaced regularly. Nozzle wear will affect gas flow and cutting quality, and dirt on the lens will cause laser beam energy loss. Therefore, regular inspection and replacement of these parts is necessary.
Ⅱ. Use the Cutting Machine Correctly
Proper use of a fiber laser cutting machine is key to extending its service life and maintaining cutting performance.
1.Operators should receive professional training and be familiar with the operating procedures and precautions of the equipment.
During operation, you should avoid overloading the equipment and set cutting parameters reasonably, such as cutting speed, laser power and gas pressure, to ensure the stability and efficiency of the cutting process.
2.Adjustment of cutting parameters:
Different materials and thicknesses require different cutting parameters. The operator should adjust the cutting parameters according to the actual situation to achieve the best cutting effect. For example, cutting thick materials requires higher laser power and lower cutting speed, while cutting thin materials requires the opposite.
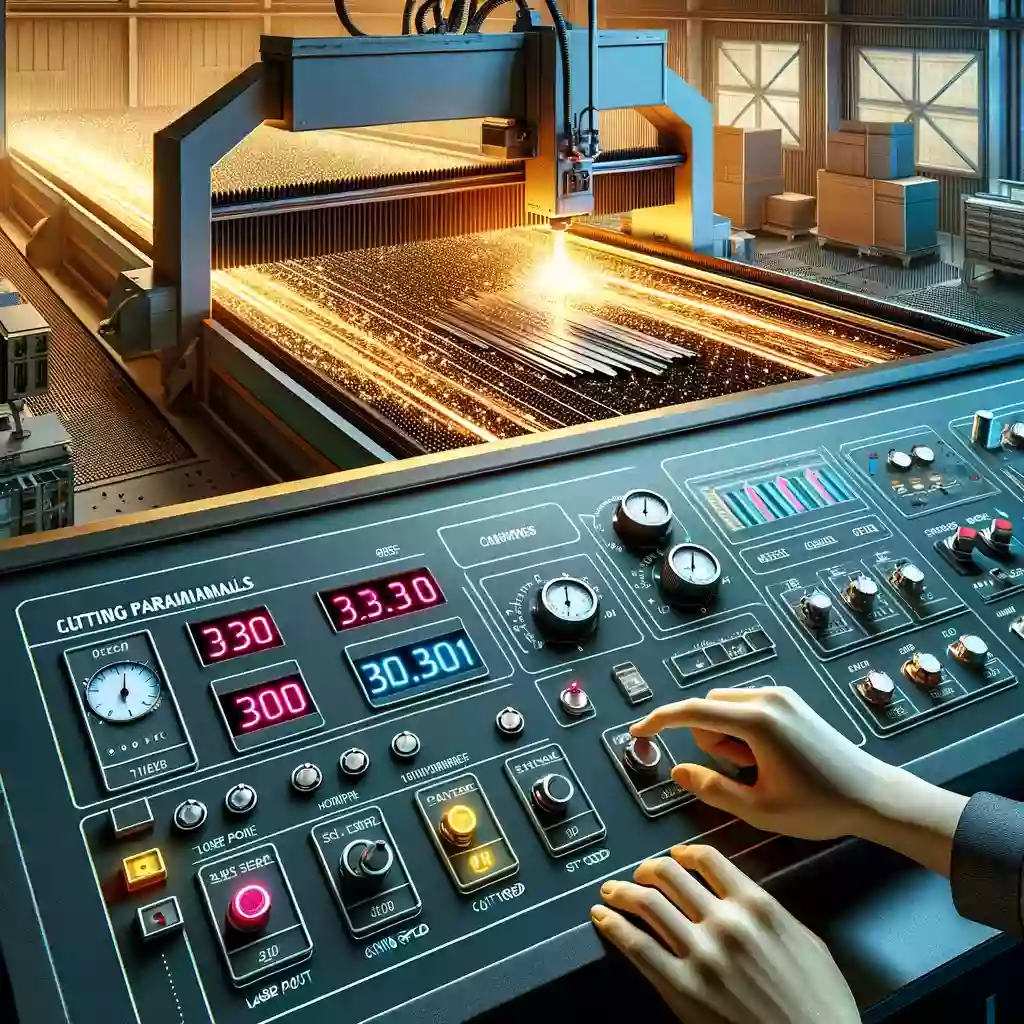
Ⅲ. Optimize Cutting Path
Optimization of cutting paths is also an important means to improve cutting performance. A reasonable cutting path can reduce cutting time, reduce equipment wear, and improve cutting quality. The following points should be considered when optimizing the cutting path:
1.Avoid repeated cuts:
The cutting path should avoid repeated cuts at the same location to prevent the material from overheating and deformation.
2.Reduce idle stroke:
Idle stroke refers to the movement of the cutting head when there is no cutting task. Reducing the idle stroke can improve cutting efficiency and reduce time waste.
Ⅳ. Control of Environmental Factors
Environmental factors also have an important impact on the performance of fiber laser cutting machines. Keeping the working environment clean and with appropriate temperature and humidity can extend the service life of the equipment and ensure the stability of cutting performance.
1.Dust prevention measures:
A large amount of dust will be generated during the cutting process. If this dust enters the inside of the equipment, it will cause damage to optical components and mechanical parts. Therefore, the working environment should be equipped with effective dust prevention equipment, such as dust collectors and air purifiers.
2.Temperature and humidity control:
Fiber laser cutting machines have certain requirements for the temperature and humidity of the working environment. Too high or too low temperature and humidity will affect the performance of the equipment. Keeping the indoor temperature at 20-25 degrees Celsius and the relative humidity between 50% and 60% is an ideal working environment.
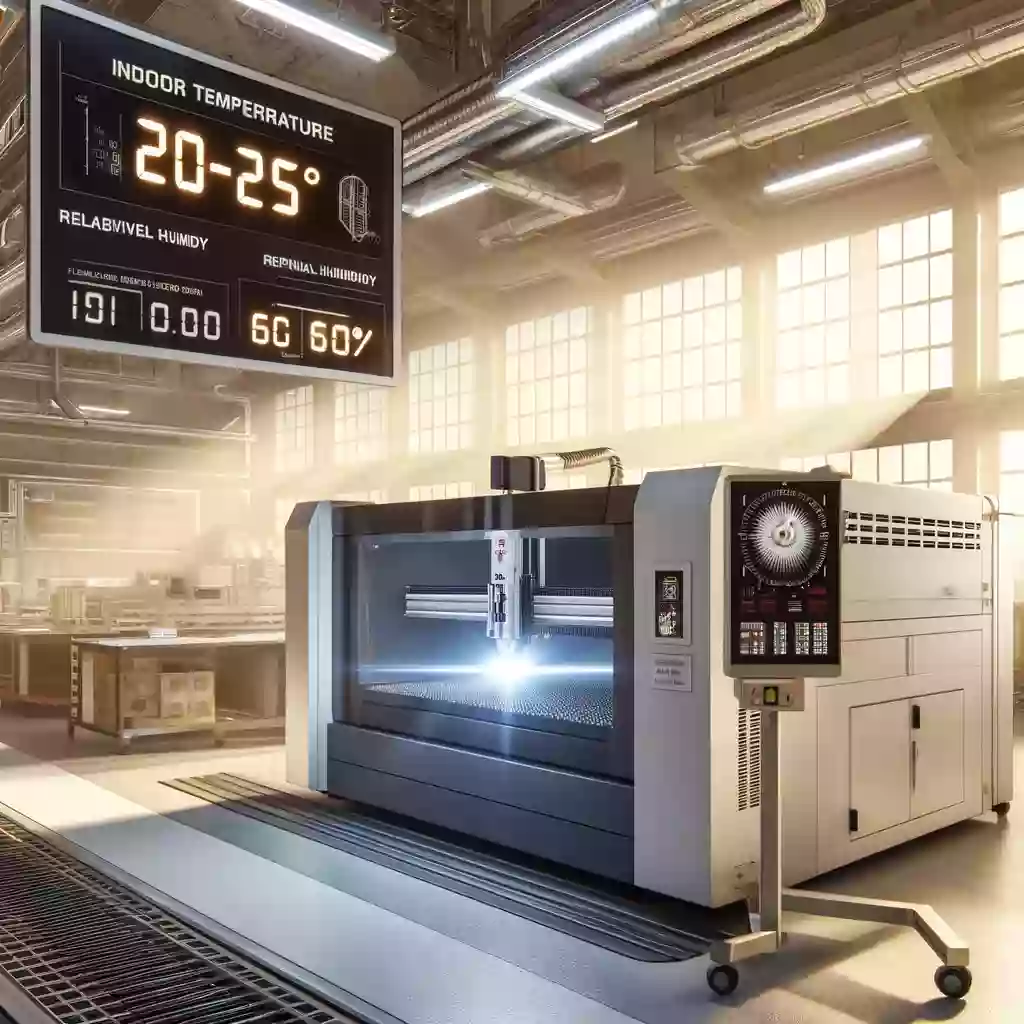
Ⅴ. Discover and Solve Problems Promptly
In daily use, operators should develop the habit of regularly checking equipment to discover and solve potential problems in a timely manner. For abnormal conditions during the operation of the equipment, such as reduced cutting quality, unstable laser output, etc., the machine should be stopped immediately for inspection to find out the cause of the problem and repair it.
1.Data monitoring:
Using modern monitoring technology to monitor the operating data of the fiber laser cutting machine in real time, abnormal conditions of the equipment can be discovered in a timely manner. For example, by monitoring parameters such as laser power, gas pressure, and cutting speed, you can determine whether the equipment is in normal working condition.
Final Thoughts
To prevent the degradation of fiber laser cutting machine’s cutting performance, it is necessary to start from many aspects such as equipment maintenance, correct use, path optimization, environmental control and problem handling. By regularly maintaining and maintaining the equipment, correctly adjusting the cutting parameters, optimizing the cutting path, controlling the temperature and humidity of the working environment, and promptly discovering and solving problems, the service life of the fiber laser cutting machine can be effectively extended and the stability of its cutting performance can be ensured, thus Improve production efficiency and product quality.