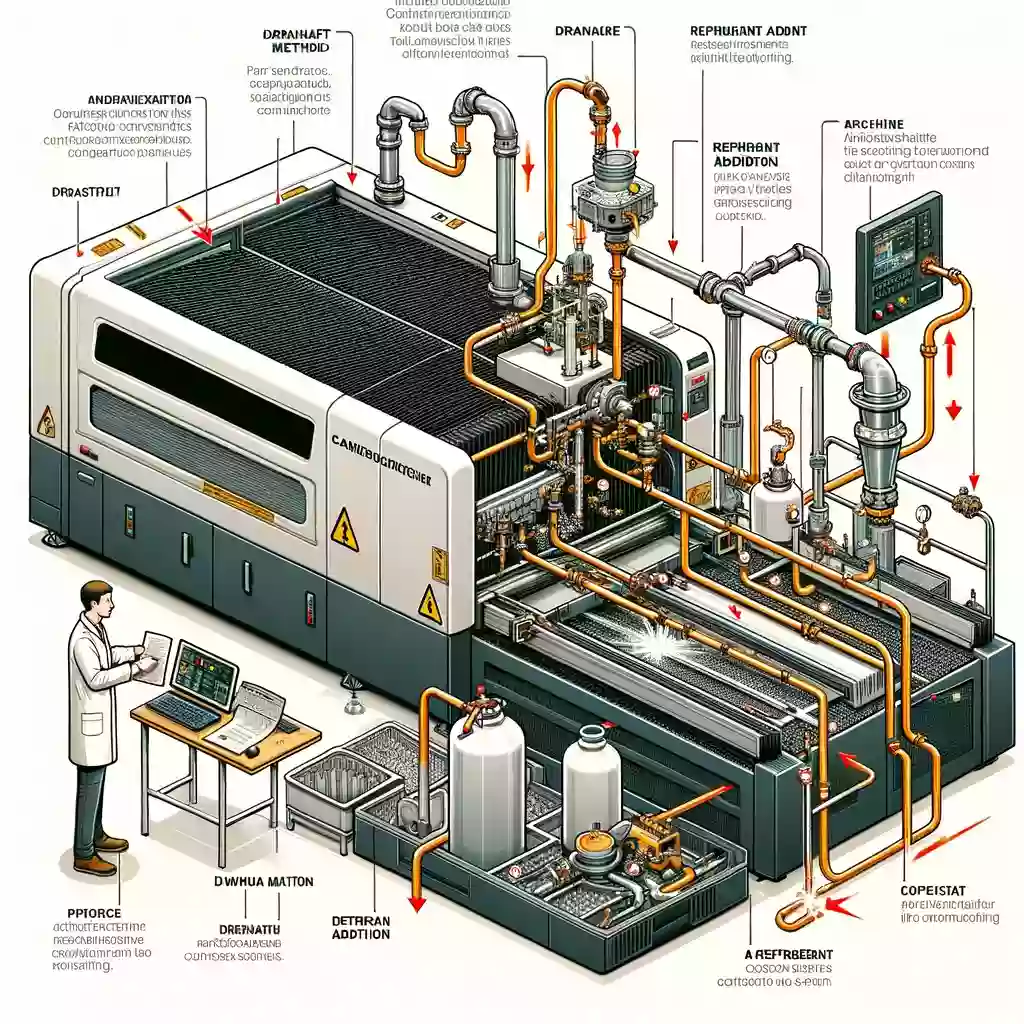
Ⅰ.Drainage Method of Fiber Laser Cutting Machine
During the use of fiber laser machine, it is necessary to regularly drain and maintain its cooling system to ensure its normal operation. The main drainage parts include: water tank, pipeline, water pump head, filter, deionization tank (optional). The following is a detailed drainage method:
1. Disconnect the power supply of the equipment involved in drainage:
First, ensure safety. Before performing any maintenance operation, disconnect the power supply of all related equipment to prevent accidental startup or electric shock accidents.
2. Water tank drainage method:
Open the drain valve or drain plug at the bottom of the water tank to drain the water in the water tank. If necessary, the water cooler can be tilted at a certain angle to ensure that the water in the water tank is discharged more thoroughly.
3. Drainage in pipelines and lasers:
First unplug the four-way water pipes. Use compressed air to blow from the drainage inlet and outlet of the pipeline for 1 minute respectively to force the stored water in the pipeline back to the water tank. Drain the forced back water through the drain port of the water tank.
4. Drainage of filter element:
Unscrew the filter element in the refrigerator and drain the water in the filter element.
5. Removal of residual water in the water tank:
Open the water tank cover and observe whether there is still water in the water tank. You can use compressed air to blow back from the water supply port again to force the residual water in the pipeline, laser (tube) and water pump back to the water tank, and then discharge it from the water tank drain port. If there is still residual water, you can slightly tilt the chiller to let the water flow out, or use a dry towel to absorb the water.
6. Drainage of the water pump head:
Unscrew the drain screw under the water pump to drain the water in the water pump. It is recommended to use compressed air to blow out the residual water in the pump head, and then tighten the drain screw.
7. Drainage of the filter and deionization tank:
Open the drain valve or plexiglass shell at the bottom of the filter and deionization tank to remove the residual water.
Ⅱ.Conditions and Methods for Adding Antifreeze to Cooling Water
In low temperature environments, antifreeze needs to be added to prevent cooling water from freezing. The following are the specific conditions and methods for adding antifreeze:
1. Selection of antifreeze:
Use ethylene glycol (also known as glycol) as antifreeze. Ethylene glycol can be purchased at local hardware and chemical stores, and is also sold online, but there may be certain restrictions on liquid transportation.
2. The mixing ratio of antifreeze and deionized water:
The recommended mixing ratio of antifreeze and deionized water is at least 30%, and the recommended ratio is 50% (i.e. 70% water and 30% ethylene glycol).
3. Conditions for adding antifreeze:
When the ambient temperature is below zero degrees (inclusive), be sure to add antifreeze to prevent the cooling water from freezing at low temperatures and damaging the equipment.
4. Precautions:
Ethylene glycol is different from ethanol (alcohol), so be sure to distinguish them to avoid using the wrong substance.
Ⅲ.Detailed Operation Steps
1. Preparation:
Make sure that the power supply of all related equipment is disconnected and the equipment is in a safe state. Prepare antifreeze (ethylene glycol) and deionized water and mix them according to the recommended ratio.
2. Drain the cooling system:
Follow the above drainage method to completely drain the cooling system of the fiber laser machine.
3. Add antifreeze mixture:
Slowly add the mixed antifreeze through the filling port of the cooling system. Make sure that the liquid fills the entire cooling system, including the water tank, pipes, filters and water pumps.
4. Inspection and adjustment:
Start the cooling system of the fiber laser cutting machine and check for leaks or abnormalities. After running for a period of time, check the antifreeze level again and replenish it if necessary.
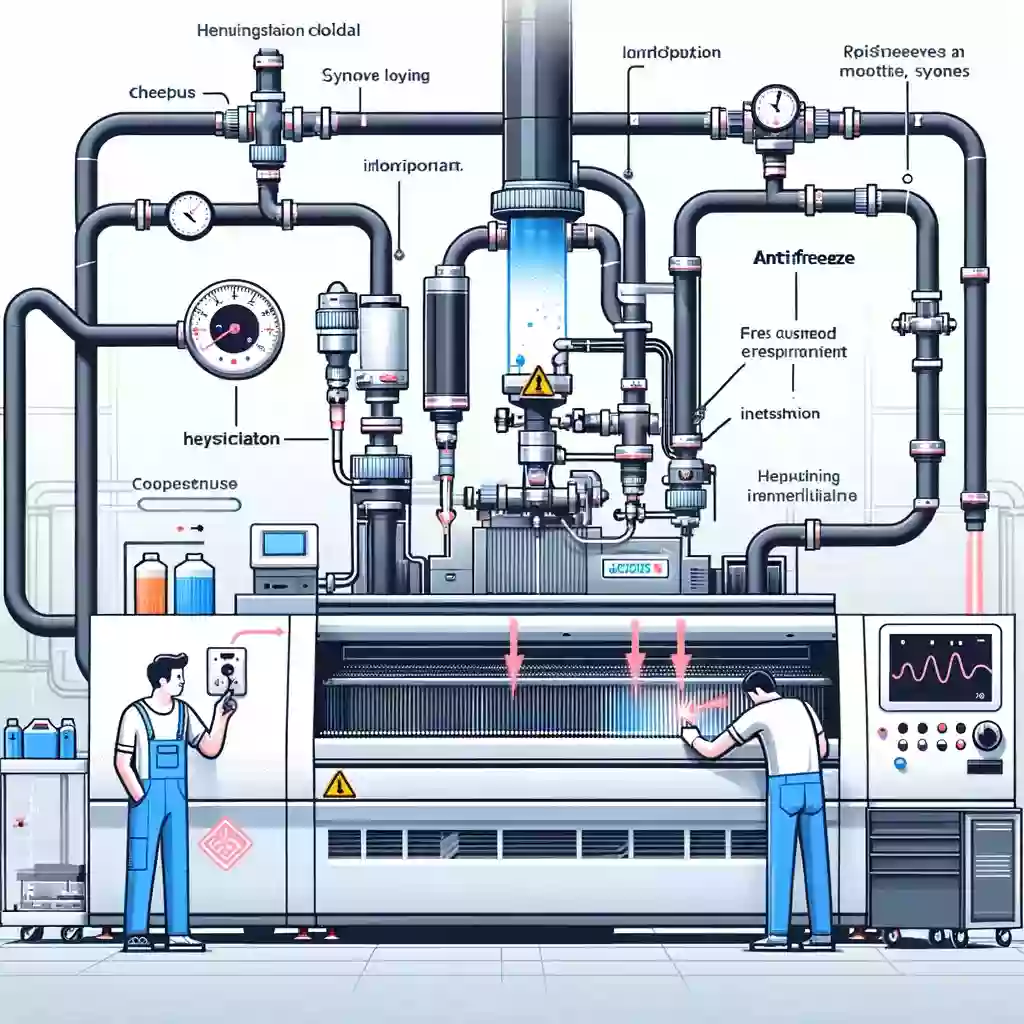
Ⅳ.The Importance of Fiber Laser Cutting Machine Maintenance
Regular maintenance and care of the fiber laser cutting machine is an important measure to ensure its efficient operation. Cleaning the cooling system and adding antifreeze can not only prevent the equipment from being damaged in a low temperature environment, but also extend the service life of the equipment and improve production efficiency. Specific maintenance measures include:
1. Regularly check the coolant:
Regularly check the coolant level and cleanliness every month, and replenish and replace the coolant in time.
2. Clean the filter:
Clean the filter of the cooling system every three months to ensure smooth flow of the coolant.
3. Maintain the water pump and pipeline:
Regularly check the working status of the water pump and pipeline to ensure that there is no leakage and blockage, and clean and replace it if necessary.
4. Antifreeze measures:
Before the cold season comes, add antifreeze in advance to ensure that the cooling system operates normally in a low temperature environment.
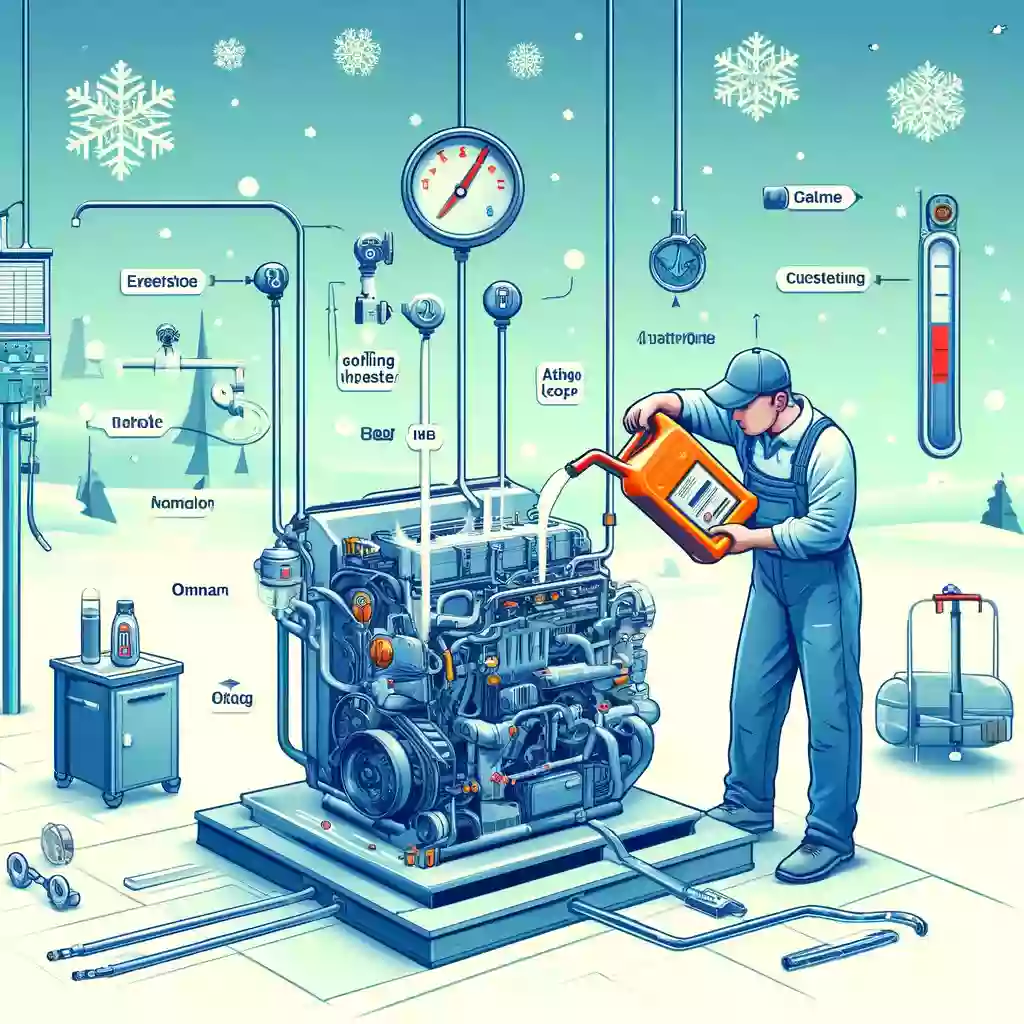
Final Thoughts
The above measures can effectively ensure the efficient and safe operation of the fiber laser cutting machine, improve production quality and efficiency, and extend the service life of the equipment. The maintenance and care of the fiber laser cutting machine is a key link for enterprises to achieve efficient production and cost control.