Fiber laser machines play a vital role in modern automobile manufacturing, especially in the production process of airbags. As a core component of vehicle safety configuration, the quality of airbags is directly related to the life safety of passengers. In order to ensure the high performance and high reliability of airbags, laser cutting machines have become a key tool in the manufacturing process with their high precision and efficiency. The application of laser cutting machines not only improves production efficiency. But also greatly improves the manufacturing quality and reliability of airbags.
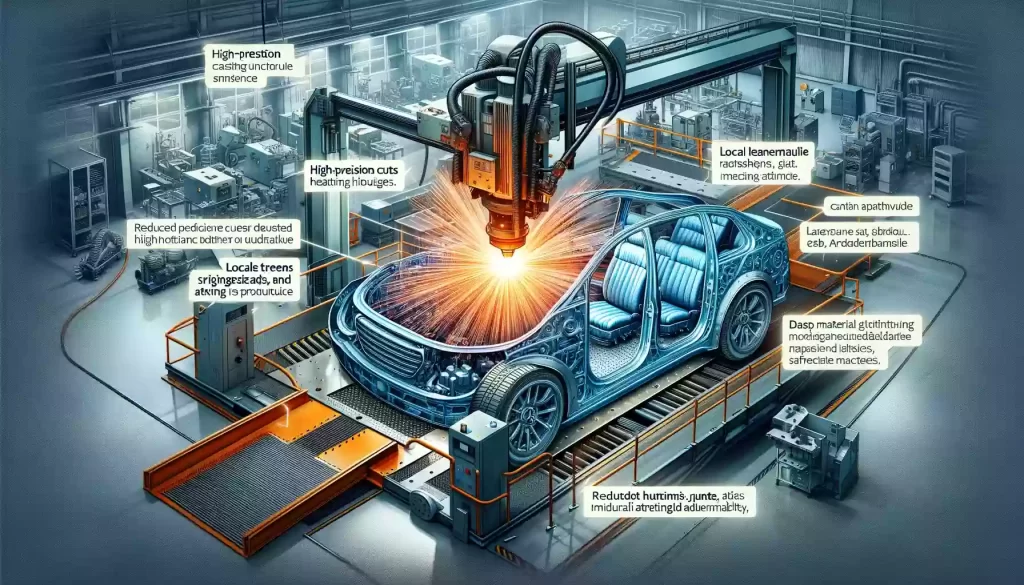
Applications
The airbag system is mainly composed of collision sensors, control modules (ECUs), gas generators and airbags. As an important part of airbags, the manufacturing quality of the gas generator shell plays a decisive role in the performance of the entire system. The fiber laser machine plays an important role in this process, which is mainly reflected in the following aspects:
1. High-precision cutting:
With its excellent precision, the laser cutting machine can ensure that every cutting surface of the gas generator shell meets strict tolerance requirements. This high-precision cutting not only improves the assembly accuracy of the gas generator. But also ensures that it can quickly and accurately deploy the airbag at the moment of collision to protect the safety of passengers.
2. Local heating, less thermal damage:
Laser cutting technology uses a local heating process. It does not produce excessive thermal effects on surrounding materials, thereby reducing the risk of thermal distortion. This feature is particularly important for airbag gas generator housings, as any slight deformation may affect their sealing and strength. The advantage of local heating not only protects the integrity of the material, but also ensures the stable performance of the gas generator.
3. Strong material adaptability:
Laser cutting machines can process a variety of materials, including stainless steel and high-strength structural steel. They are often used to manufacture gas generator housings. The good compatibility of different materials during the laser cutting process enables manufacturers to select the best material according to specific needs. Further improving the overall performance of the airbag. The diversity of materials enables laser cutting machines to show excellent cutting effects in different application scenarios.
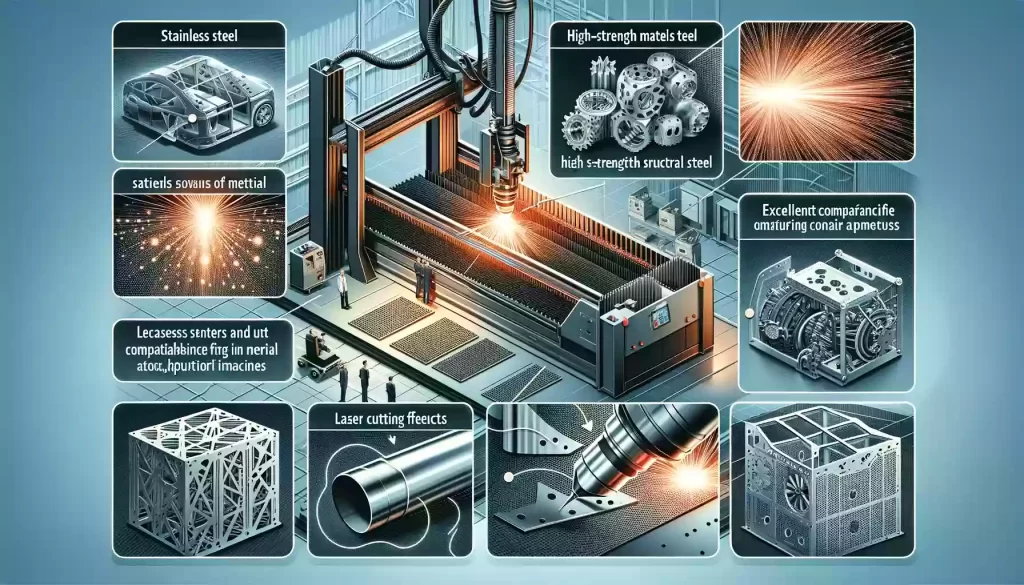
4. No impurities and no pollution:
No filling materials are required during the laser cutting process. It means that the cutting surface will not be contaminated by impurities, maintaining the purity of the material. This feature not only improves the welding quality, but also effectively avoids potential pollution problems, helping to extend the service life of the gas generator. The pure cutting surface helps to improve the sealing and safety of the gas generator.
5. Efficient production:
The high efficiency of the laser cutting machine enables it to complete a large number of cutting tasks in a short time. For automobile manufacturers, this means that it can greatly improve production efficiency, shorten production cycles, and meet the huge market demand for high-quality airbags. Efficient production capacity not only improves the competitiveness of enterprises, but also responds to changes in market demand in a timely manner.
6. Environmental protection and energy saving:
Compared with traditional cutting methods, laser cutting technology is more environmentally friendly and energy-saving. Its efficient energy utilization and low pollution emissions not only meet the environmental protection requirements of modern industrial production, but also reduce the energy consumption and operating costs of enterprises. The environmental protection characteristics of the laser cutting machine make it an important driving force for sustainable development.
7. High bonding strength:
The airbag gas generator manufactured using laser cutting technology has extremely high bonding strength. The bonding strength after laser welding can make its water pressure resistance reach 70MPa (depending on the material). It greatly improves the safety and reliability of the airbag system. High bonding strength ensures the stability and reliability of the airbag under high pressure.
8. Good repetitive operation stability:
Laser cutting technology has shown excellent repetitive operation stability in mass production. And the cutting results are consistent each time, which is particularly important for airbag gas generators that need to be mass-produced. Stable and repetitive operation performance ensures the high quality and consistency of each product.
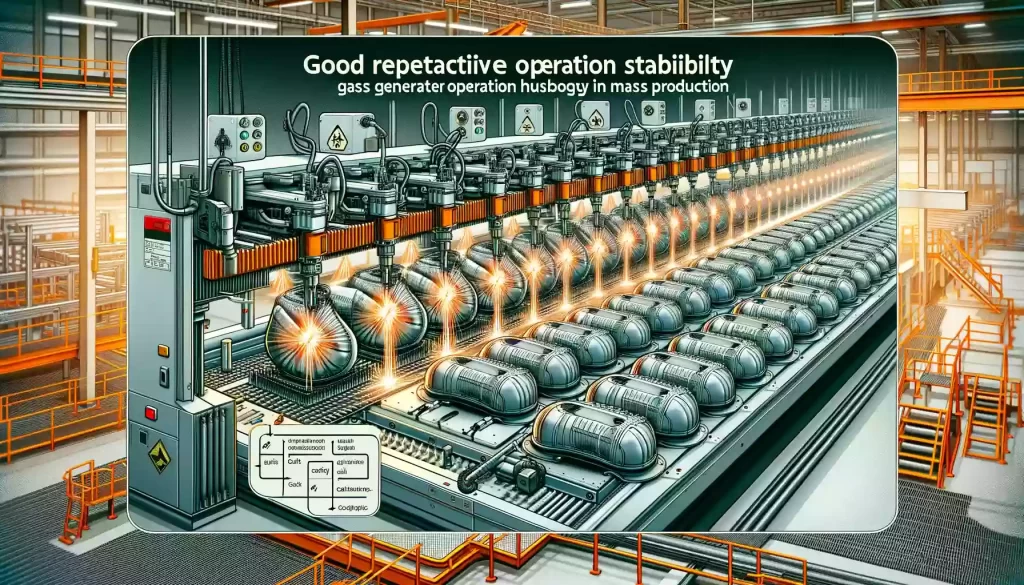
Final Thoughts
In summary, the laser cutting machine plays an irreplaceable role in the manufacturing process of automobile airbags. Its high precision, high efficiency and environmental protection characteristics not only improve the manufacturing quality and reliability of airbags, but also promote the progress of automobile manufacturing technology. In the future, with the continuous development of laser cutting technology, we have reason to believe that the performance and safety of automobile airbags will be further improved, providing more reliable protection for passengers. As a key technical means in this process, the laser cutting machine will continue to lead the development of automobile safety technology. And bring us a safer travel experience. Through continuous technological innovation and application, the laser cutting machine will demonstrate its unique advantages and broad application prospects in more fields.