Fiber laser machines have been widely used in modern manufacturing industry because of their efficient and precise cutting capabilities. However, when using a fiber laser cutting machine, the cutting speed is a critical operating parameter that has a crucial impact on the cutting results. This article will explore how the cutting speed of a fiber laser cutting machine affects the cutting effect and propose ways to optimize the cutting speed.
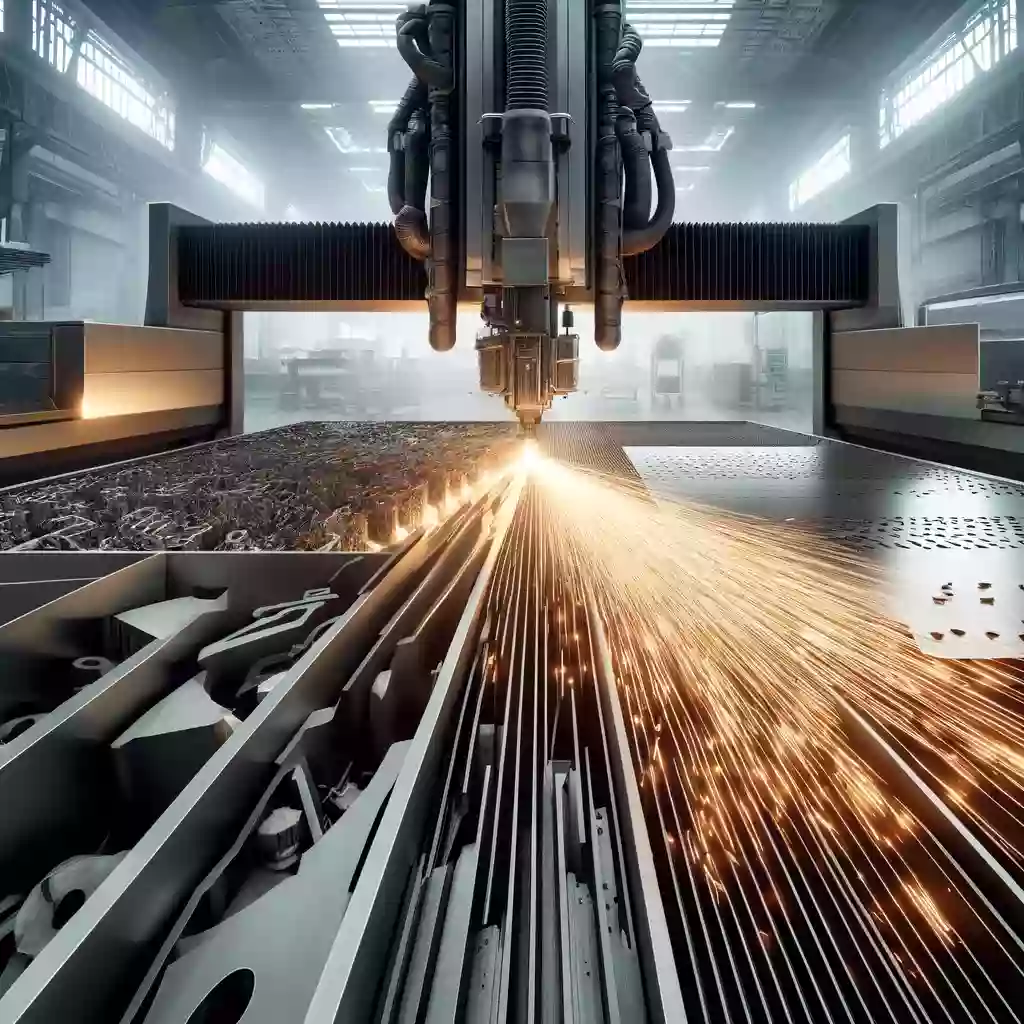
Ⅰ.Influence of Cutting Speed on Cutting Quality
1. Cutting speed and cutting accuracy:
The cutting speed directly affects the accuracy of the cutting. When the cutting speed is too fast, the laser beam does not stay on the surface of the workpiece for a sufficient time. It can easily lead to uneven cutting edges, burrs, tailing and other defects. On the contrary, if the cutting speed is too slow, the laser beam will stay on the surface of the workpiece for too long. It will cause excessive melting and widening of the cutting gap, which will affect the accuracy and aesthetics of the cutting.
2. Cutting speed and cutting quality:
The speed of the cut will also affect the quality of the cut. The appropriate cutting speed ensures a smooth, burr-free cutting surface with a high degree of verticality of the cut. If the cutting speed is too fast, the laser energy cannot fully act on the material. Resulting in impermeable or incomplete cutting. If the cutting speed is too slow and the laser energy is too concentrated, the material may be over-melted. The cutting edge is rough, and even the burning phenomenon may occur.
3. Cutting speed and material characteristics:
Different materials are less sensitive to cutting speeds. In general, thin plate materials can be cut relatively quickly, while thick plate materials require slower cutting speeds to ensure adequate cutting. For example, when cutting stainless steel and carbon steel, due to the different thermal conductivity and melting point of the material, the cutting speed needs to be adjusted according to the actual situation to get the best cutting effect.
Ⅱ.Optimization Method of Cutting Speed
1. Determine reasonable cutting parameters:
When using a fiber laser machine, reasonable cutting parameters are the key to ensure the quality of the cut. The operator should adjust the cutting speed, laser power, focus position and other parameters. According to the type and thickness of the material to be cut, as well as the expected cutting quality. Usually, laser cutting machine manufacturers will provide cutting parameter tables for different materials. And operators can refer to these parameters for preliminary settings, and continuously adjust and optimize in actual operation.
2. Perform a cutting test:
In order to determine the optimal cutting speed, the operator can perform a cutting test. By cutting on the same piece of material at different speeds, compare the cutting results at each cutting speed to find the optimal cutting speed. The cutting test not only helps the operator to understand the effect of different speeds on the cutting effect. But also accumulates experience for actual production.
3. Take advantage of intelligent control technology:
Modern fiber laser cutting machines are usually equipped with advanced intelligent control systems that can monitor and adjust the cutting speed in real time. These systems are able to automatically adjust the cutting parameters based on feedback from the material to ensure the stability and quality of the cutting process. For example, some intelligent systems can monitor temperature changes during the cutting process through sensors and automatically adjust the cutting speed based on temperature feedback to avoid overheating or impermeable material.
4. Regular maintenance and maintenance of equipment:
The performance stability of the fiber laser cutting machine is also crucial for the optimization of the cutting speed. Regular maintenance and maintenance of equipment to ensure the normal operation of key components such as lasers, lenses, and cutting heads can avoid cutting quality problems caused by equipment failure. At the same time, keeping the optical path system clean and stable also helps to improve cutting efficiency and cutting quality.
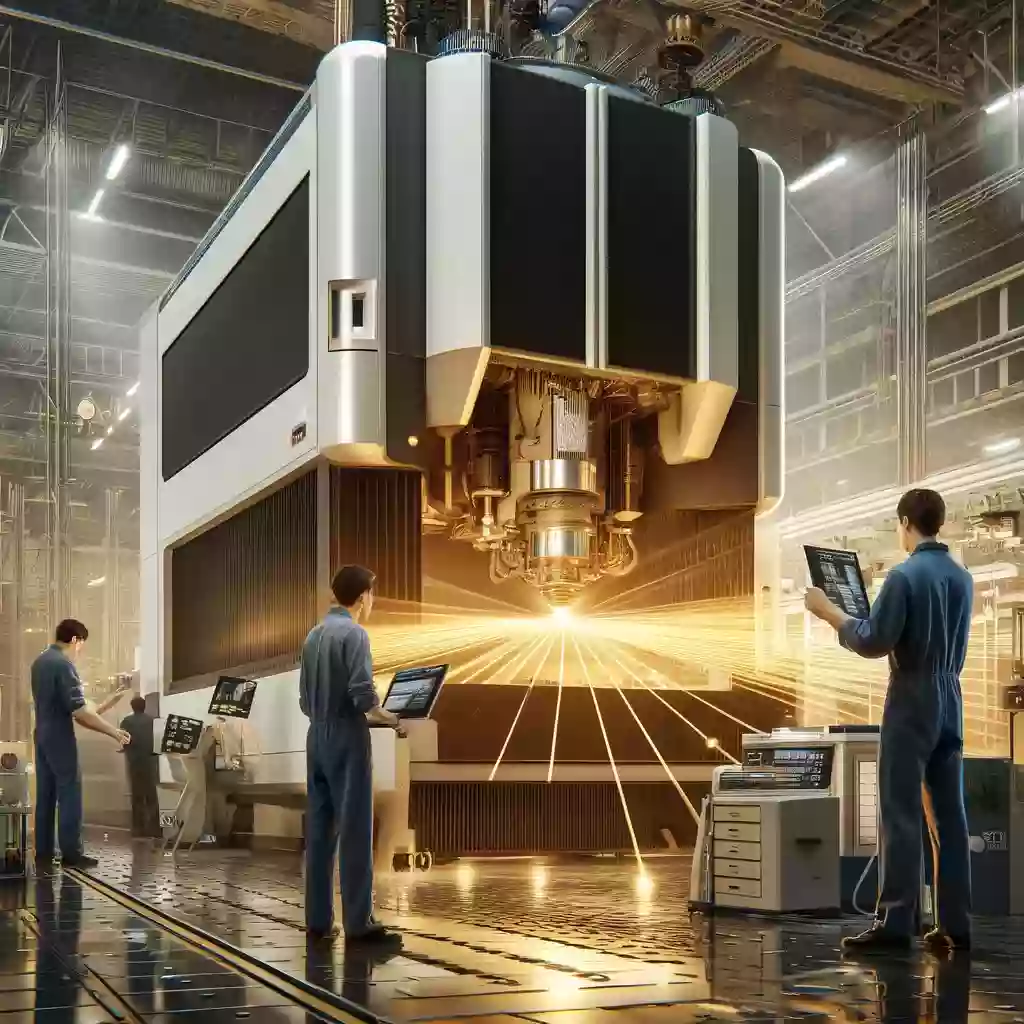
Ⅲ.Specific Influence of Cutting Speed on Different Materials
1. Stainless steel:
Stainless steel is a common material in the industry, and its cutting speed has a significant impact on the cutting effect. In general, thinner stainless steels can be cut at a faster speed to guarantee efficient production. For thicker stainless steels, the cutting speed needs to be reduced appropriately to ensure the complete cut and the quality of the cut surface.
2. Carbon steel:
Carbon steel has good thermal conductivity and can be cut relatively quickly. However, for carbon steel with a large thickness, the cutting speed is too fast and may lead to impermeable cutting, and the speed must be reduced to ensure the thoroughness of the cutting and the smoothness of the cutting surface.
3. Aluminum alloy:
Aluminum alloys are relatively fast to cut, but due to their low melting point, they are prone to slag when cutting. It is necessary to adjust the laser power and auxiliary gas while ensuring the cutting speed to reduce the generation of slag and ensure the cutting quality.
4. Non-metallic materials:
For non-metallic materials such as plastics and ceramics, the effect of cutting speed is also significant. Cutting too fast for plastic materials can cause the cutting edges to melt, while ceramic materials require a slower speed to avoid cracking.
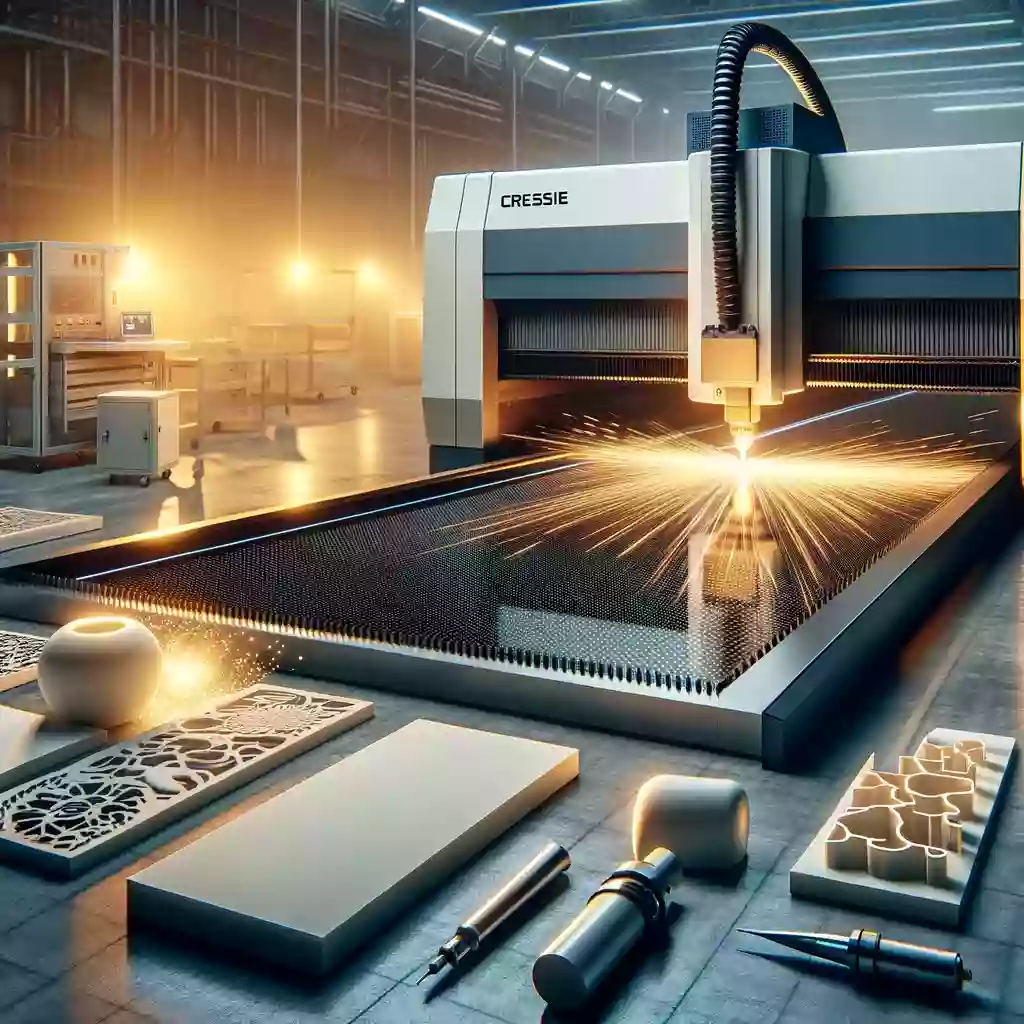
Final Thoughts
The cutting speed of the fiber laser cutting machine has an important impact on the cutting effect. In practical application, the operator should reasonably adjust the cutting speed according to the characteristics of different materials and specific cutting requirements, and continuously optimize the cutting parameters through cutting tests, intelligent control and equipment maintenance to obtain the best cutting results. Only in this way can we give full play to the advantages of fiber laser cutting machine and improve production efficiency and product quality.