With the continuous development of the manufacturing industry, cutting technology has been widely applied across various sectors. As an advanced cutting technology, laser cutting machines are gradually replacing many traditional cutting methods. This article will comprehensively compare fiber laser machines and traditional cutting methods in various aspects, exploring their respective advantages, applicable scenarios, and future development trends.
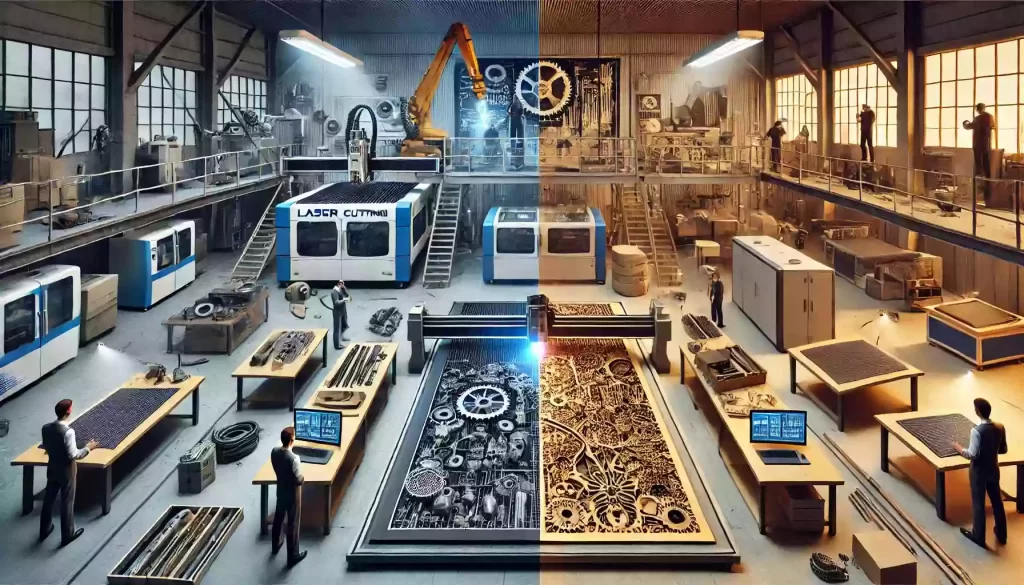
Ⅰ.Principles and Basic Characteristics
1.Technical principle of laser cutting machines:
Fiber laser machines use high-power laser beams to irradiate the material surface, causing the material to quickly melt, burn, or vaporize. High-pressure gas is then used to blow away the molten material, forming a cut. Laser cutting is characterized by high precision, high speed, and non-contact processing, and is widely used for cutting materials such as metals, plastics, wood, and cardboard.
2.Technical principle of traditional cutting methods:
Traditional cutting methods include mechanical cutting, stamping, and sawing. These methods typically rely on mechanical tools to apply pressure or shear force to the material. Traditional cutting methods are advantageous for their simple equipment and easy operation but have certain limitations in terms of precision, efficiency, and material adaptability.
Ⅱ.Comparison of Precision and Cutting Quality
1.Precision and cutting quality of laser cutting machines:
Laser cutting machines can achieve micron-level precision, producing smooth and clean cutting edges without the need for secondary processing. Their non-contact cutting method avoids the impact of mechanical stress on materials, making them suitable for high-precision and high-requirement cutting tasks.
2.Precision and cutting quality of traditional cutting methods:
The precision of traditional cutting methods mainly depends on the accuracy of the tools and the stability of the operation. Due to the contact nature of mechanical cutting, cutting edges often have burrs and deformations, especially when cutting hard materials. These issues usually require additional post-processing steps to correct the cut quality.
Ⅲ.Comparison of Cutting Speed and Efficiency
1.Speed and efficiency of laser cutting machines:
Laser cutting machines have very high cutting speeds, particularly excelling in the cutting of thin materials and complex patterns. Their efficient cutting process can significantly increase production efficiency and reduce processing time.
2.Speed and efficiency of traditional cutting methods:
Traditional cutting methods have relatively slower cutting speeds, especially when dealing with complex shapes or thick materials, resulting in lower efficiency. Additionally, the wear and replacement of mechanical tools can affect the continuity and efficiency of cutting operations.
Ⅳ.Comparison of Material Adaptability and Flexibility
1.Material adaptability and flexibility of laser cutting machines:
Laser cutting machines are suitable for various materials, including metals, non-metals, and composites. Their cutting capabilities are not limited by the hardness or thickness of the material and can handle various complex shapes and details, offering high flexibility and broad applicability.
2.Material adaptability and flexibility of traditional cutting methods:
Traditional cutting methods have relatively poor material adaptability, especially when dealing with high-hardness or thin materials, leading to processing difficulties and quality issues. Additionally, traditional cutting methods have lower flexibility in handling complex patterns and fine details.
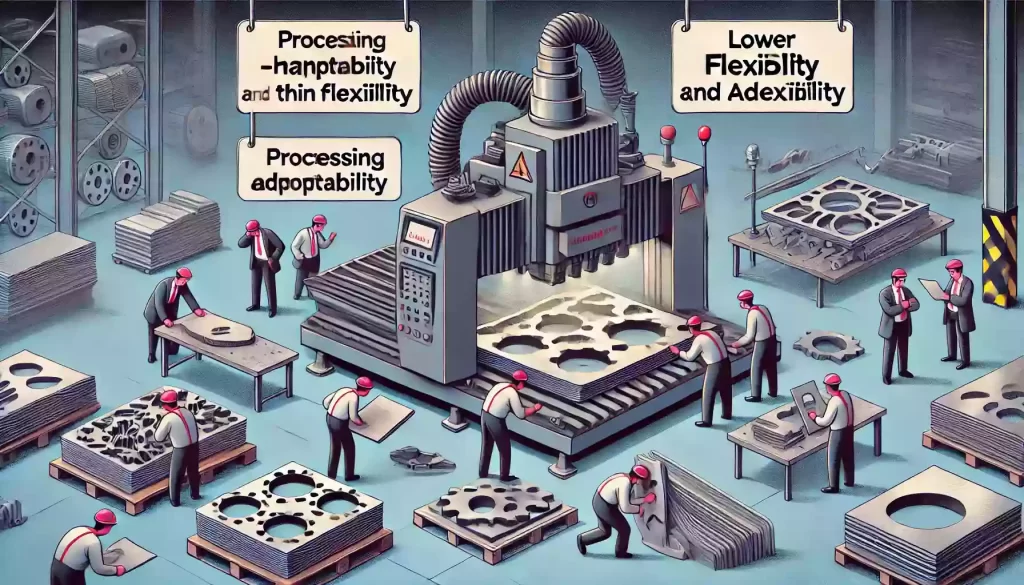
Ⅴ.Comparison of Cost and Maintenance
1.Cost and maintenance of laser cutting machines:
Laser cutting machines have a high initial investment, but their efficient production capabilities and low maintenance requirements can reduce overall costs in the long run. The main maintenance tasks for laser cutting machines include cleaning the optical system and maintaining the laser source, which are relatively straightforward.
2.Cost and maintenance of traditional cutting methods:
Traditional cutting methods have lower equipment costs but higher tool wear, requiring frequent replacement and maintenance. The replacement and maintenance of tools not only increase material costs but also affect the continuity and efficiency of production.
Ⅵ.Comparison of Environmental Protection and Safety
1.Environmental protection and safety of laser cutting machines:
The non-contact cutting process of laser cutting machines reduces the generation of waste and environmental pollution. The small heat-affected zone during laser cutting minimizes material deformation and damage. Laser cutting machines also offer high safety, with enclosed processing environments and protective measures effectively safeguarding operators.
2.Environmental protection and safety of traditional cutting methods:
Traditional cutting methods generate a lot of waste and dust during the cutting process, increasing environmental pollution risks. The operational safety of mechanical cutting is lower, with operators being more prone to mechanical injuries, necessitating stringent protective measures.
Ⅶ.Future Development Trends
1.Development trends of laser cutting technology:
In the future, laser cutting technology will progress towards higher power, higher precision, and greater intelligence. The development and application of new types of lasers will further improve the efficiency and quality of laser cutting. The integration of artificial intelligence and automation technology will enable laser cutting machines to have higher autonomous decision-making and adaptive capabilities, catering to more complex and diversified processing needs.
2.Development trends of traditional cutting methods:
Although traditional cutting methods lag behind laser cutting in many aspects, their simplicity and cost-effectiveness still hold market demand. In the future, traditional cutting methods will increasingly integrate modern numerical control technology to enhance processing precision and efficiency. The incorporation of environmental protection and safety technology will also drive the optimization and improvement of traditional cutting methods.
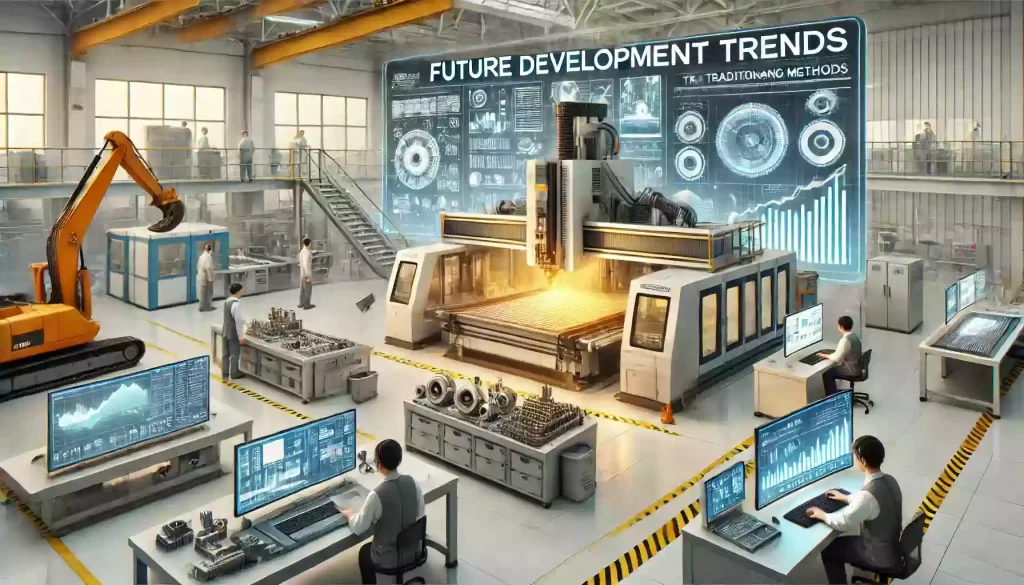
Final Thoughts
Laser cutting machines and traditional cutting methods each have their advantages and disadvantages. Laser cutting machines excel in high-precision, high-efficiency, and versatile material adaptability, making them outstanding in many high-demand processing fields. Meanwhile, traditional cutting methods remain competitive in specific scenarios due to their simple equipment, ease of operation, and low cost. In the future, both technologies will continue to evolve in their respective directions, providing diverse solutions for the manufacturing industry.