Laser cutting has become essential in the machining of ultra-hard materials. However, it poses significant challenges due to the material’s durability. A high-quality laser cutting machine requires precise control to achieve desired results. Moreover, optimization strategies are crucial for effective processing.
I. Understanding Ultra-Hard Materials
Ultra-hard materials like diamond, ceramics, and tungsten carbide are tough to machine. Traditional cutting methods struggle to handle these materials efficiently. They often cause cracks, chips, or material loss. Therefore, manufacturers increasingly turn to laser cutting. The laser cutting machine offers a non-contact method, reducing the risk of mechanical stress.
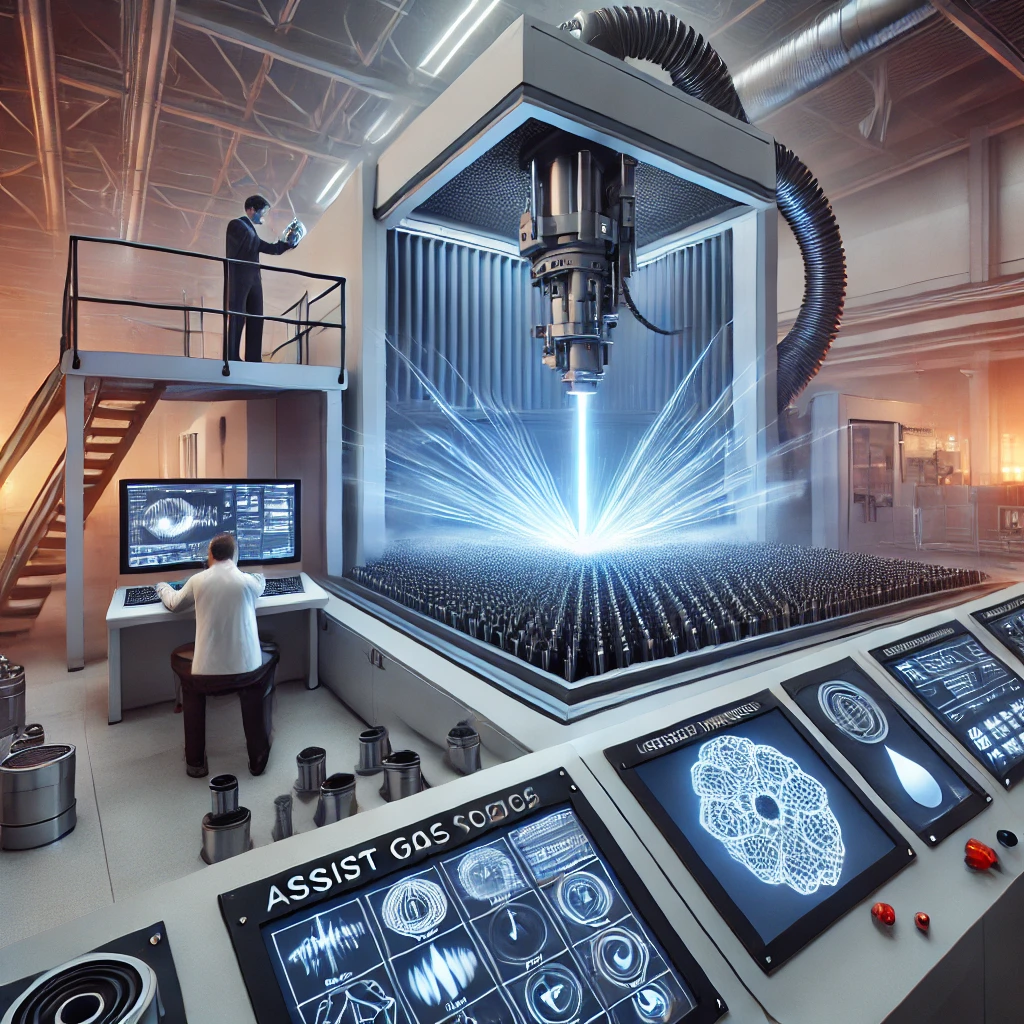
II. The Role of Precision Control
Precision control is vital when cutting ultra-hard materials. The laser’s power and speed must be carefully adjusted. Higher power increases cutting speed but can cause material damage. Conversely, lower power minimizes damage but slows the process. Thus, operators must find the right balance.
A laser machine manufacturer typically provides software with advanced control settings. These settings allow operators to adjust parameters like pulse duration and frequency. Fine-tuning these factors can enhance the cutting process. For example, adjusting the pulse rate can reduce heat-affected zones. As a result, it prevents cracks in materials like ceramics.
III. Optimizing the Laser Cutting Process
Successful laser cutting involves several optimization strategies. First, selecting the correct laser type is essential. Different laser cutting machines use various lasers, such as CO2 or fiber lasers. Fiber lasers work best for ultra-hard materials. They produce a more concentrated beam, allowing for precision cuts.
Moreover, the use of assist gases like oxygen or nitrogen can optimize the cutting process. These gases help blow away molten material from the cutting area. This improves edge quality and reduces the need for post-processing. Additionally, a laser machine manufacturer might recommend specific gases based on material type.
IV. Key Techniques for Cutting Ultra-Hard Materials
Several techniques can optimize the cutting of ultra-hard materials. One effective method is multiple-pass cutting. Instead of making a single deep cut, the laser cutting machine makes several shallow passes. This reduces the stress on the material, preventing cracks or warping. Multiple-pass cutting is particularly beneficial for thick ceramics and tungsten carbide.
Another technique involves controlling the focal point of the laser. By focusing the beam at different depths, operators can adjust the cut’s precision. This is crucial when working with uneven surfaces. Adjusting the focal point ensures consistent quality across the material.
V. Cooling Systems and Their Importance
Ultra-hard materials require careful thermal management during cutting. Excessive heat can cause fractures in materials like glass or diamond. Therefore, using an appropriate cooling system is necessary. Many laser machine manufacturers integrate cooling systems into their machines. These systems use water or air to maintain a stable cutting environment.
Furthermore, applying a cooling strategy during cutting can improve the lifespan of the laser cutting machine. It prevents overheating, thus avoiding potential damage to the laser components. Consistent cooling also results in smoother cuts with minimal heat-affected zones.
VI. Automation and Real-Time Monitoring
Automation enhances the precision of laser cutting. Many modern laser cutting machines come equipped with automated control systems. These systems monitor the cutting process in real-time. Sensors detect changes in material thickness and adjust laser parameters accordingly.
For example, if the material’s density varies, the laser cutting machine can automatically adjust its power. This prevents issues like incomplete cuts or excessive burning. Automation also reduces human errors, improving overall production quality. As a result, it ensures a higher success rate in processing ultra-hard materials.
VII. Regular Maintenance and Calibration
Routine maintenance is vital for optimal performance. A laser machine manufacturer usually provides maintenance guidelines. Following these instructions can extend the machine’s lifespan. Regularly cleaning the lenses, mirrors, and nozzles prevents debris buildup. Proper alignment and calibration ensure the laser maintains its precision.
Calibration is especially important for cutting ultra-hard materials. Small deviations in the laser’s alignment can result in faulty cuts. Periodic checks help maintain the machine’s accuracy. Investing time in maintenance reduces costly repairs and downtime.
VIII. Collaboration with Laser Machine Manufacturers
Collaborating with a reputable laser machine manufacturer offers significant advantages. Manufacturers provide expert guidance on machine setup and operation. They may offer training sessions for operators. This training can improve the efficiency of the cutting process.
Additionally, manufacturers often update their software with new features. These updates can include enhanced control options or improved safety measures. Staying up-to-date with these advancements keeps the laser cutting machine at peak performance. It allows operators to use the latest techniques for ultra-hard material processing.
IX. Adopting Cutting-Edge Technology
New technologies continue to improve laser cutting capabilities. For instance, some laser cutting machines now use adaptive optics. These optics adjust the laser beam’s shape and size in real-time. This capability optimizes the cutting of ultra-hard materials, providing smoother edges.
Similarly, hybrid lasers combine different wavelengths for better precision. A laser machine manufacturer might develop such advanced systems. They aim to offer solutions tailored to complex materials. Adopting these technologies can enhance competitiveness in industries working with ultra-hard materials.
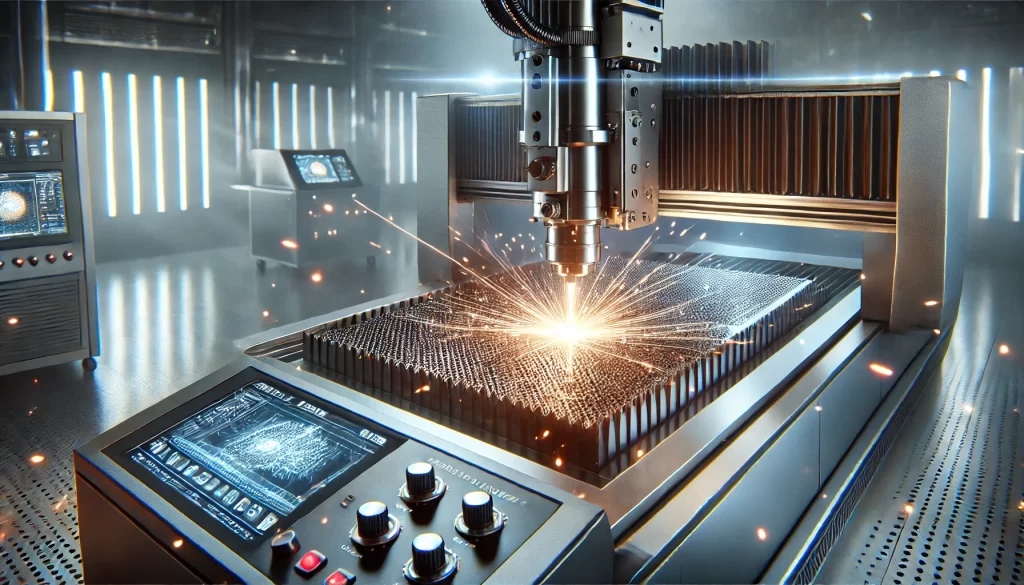
X. Conclusion
Processing ultra-hard materials with a laser cutting machine demands precision control and optimization. Techniques like multiple-pass cutting, focal point adjustment, and cooling systems improve outcomes. Collaboration with a reputable laser machine manufacturer provides valuable expertise and support.
By embracing automation and adopting new technologies, manufacturers can achieve superior results. Regular maintenance and calibration further ensure consistent performance. In this way, laser cutting becomes a reliable and efficient method for ultra-hard material processing. As technology advances, these strategies will continue to evolve, providing even greater possibilities for precision and control.