In modern manufacturing, fiber laser machine is popular for its high precision and efficiency. As technology advances, laser developments continue to evolve, particularly with regard to the duration of laser pulses. Nanosecond (ns), picosecond (ps) and femtosecond (fs) lasers are typical representatives. And they each have their own advantages in the accuracy and efficiency of material processing. This article will explore in detail the different applications and performance of these three lasers in laser cutting.
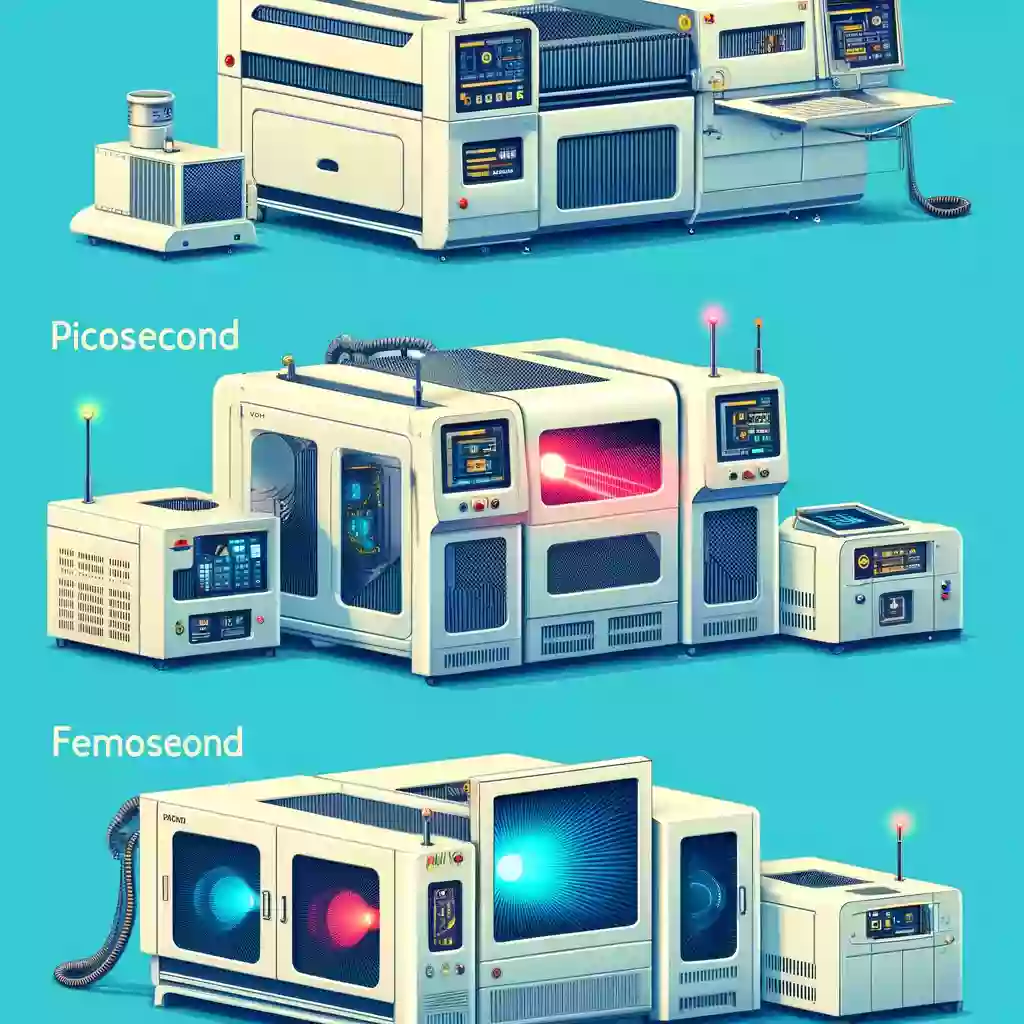
Ⅰ. Principles and Concepts
1.Nanosecond laser cutting:
Nanosecond laser, its pulse width is usually in the nanosecond level, that is, 10^-9 seconds. The main advantages of nanosecond lasers are their high energy density and good penetration. These features allowing them to quickly cut thick materials. However, due to the long pulse duration, nanosecond laser processing may produce a large heat-affected zone. This may cause thermal damage or deformation of the material.
2.Picosecond laser cutting:
The pulse width of picosecond laser is at the picosecond level, that is, 10^-12 seconds. Compared to nanosecond lasers, picosecond lasers offer shorter pulse durations, which reduces the heat-affected zone on the material surface, thereby reducing thermal damage. Picosecond lasers are particularly suitable for materials that require fine processing, such as thin films, thin lines, and complex microstructures. In addition, picosecond lasers are able to provide higher processing accuracy, making them very useful in the fields of microelectronics and precision engineering.
3.Femtosecond laser cutting:
Femtosecond laser is one of the laser types with the shortest pulse duration at present, and the pulse width can reach the femtosecond level, that is, 10^-15 seconds. The extremely short pulse duration of femtosecond lasers virtually eliminates the heat-affected zone, allowing it to process a variety of materials with little thermal damage. This laser is particularly suitable for ultra-fine processing, such as cutting of semiconductor materials, biological tissue and other sensitive materials that are susceptible to thermal damage. Due to its superior processing quality and precision, femtosecond lasers are increasingly used in scientific research and high-end manufacturing.
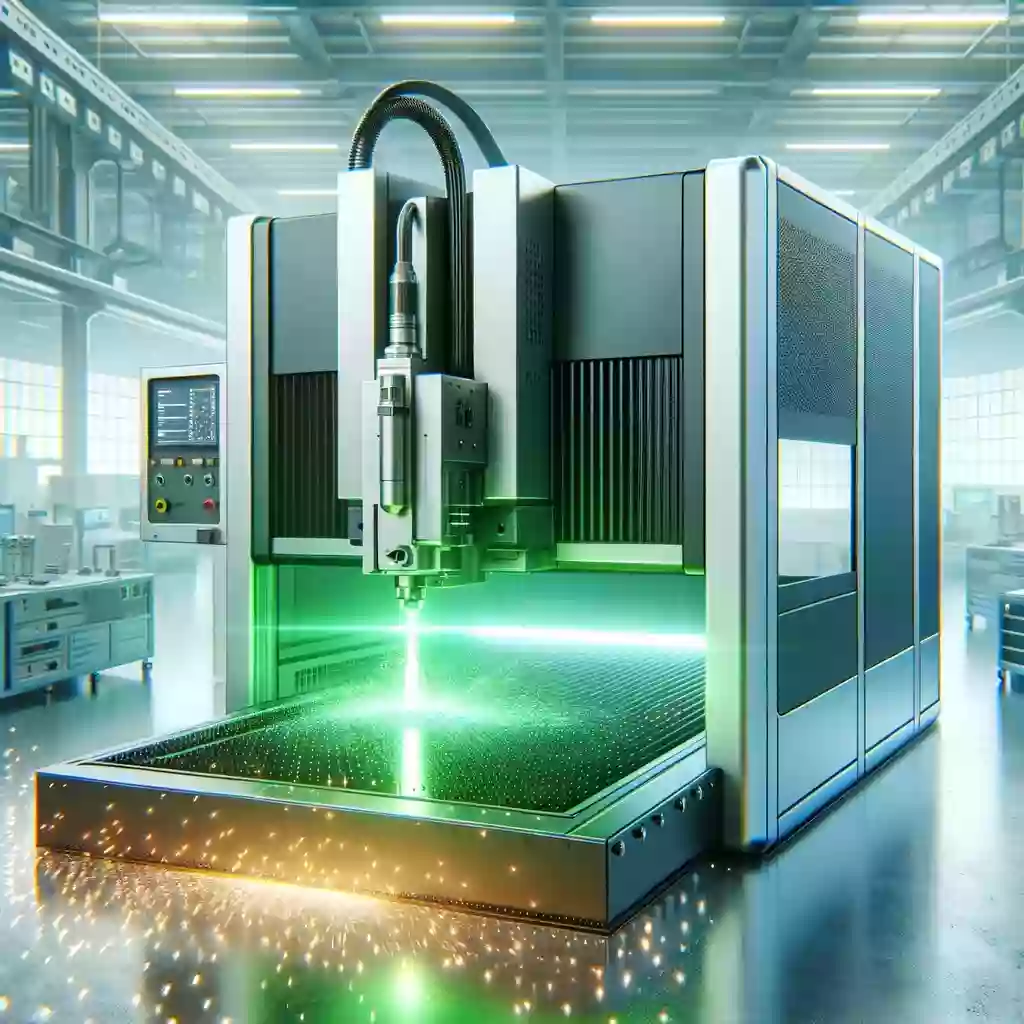
Ⅱ. Differences in Processing Scale
The choice of nanosecond, picosecond and femtosecond lasers in laser cutting mainly depends on the material type and the required processing quality. Nanosecond lasers are suitable for large-scale, rapid processing, especially when thermal damage is not a major issue. Picosecond lasers perform better in processing tasks that require higher precision and smaller heat-affected zones. Femtosecond lasers are the best choice when extremely high precision and minimal thermal impact are required.
Ⅲ. Differences in Processing Materials:
Under different processing conditions, the time units selected are different, so there are naming rules for nanosecond, picosecond, and femtosecond laser equipment. For example, nanosecond UV laser cutting machines are often used for processing thin film materials, picosecond UV laser cutting machines are often used for processing brittle materials, and femtosecond UV laser cutting machines are used for processing conductive thin film oxides and other materials. This type of laser is mainly used for traditional material processing, such as cutting and engraving metals, plastics and ceramics.
Ⅳ. Differences in Processing Applications:
1.Picosecond laser can be used in laser drilling
Laser drilling is one of the common applications of picosecond laser. Picosecond laser can complete the hole processing by impact drilling and ensure the uniformity of the hole. In addition to circuit boards, picosecond lasers can also perform high-quality drilling on materials such as plastic films, semiconductors, metal films, and sapphire.
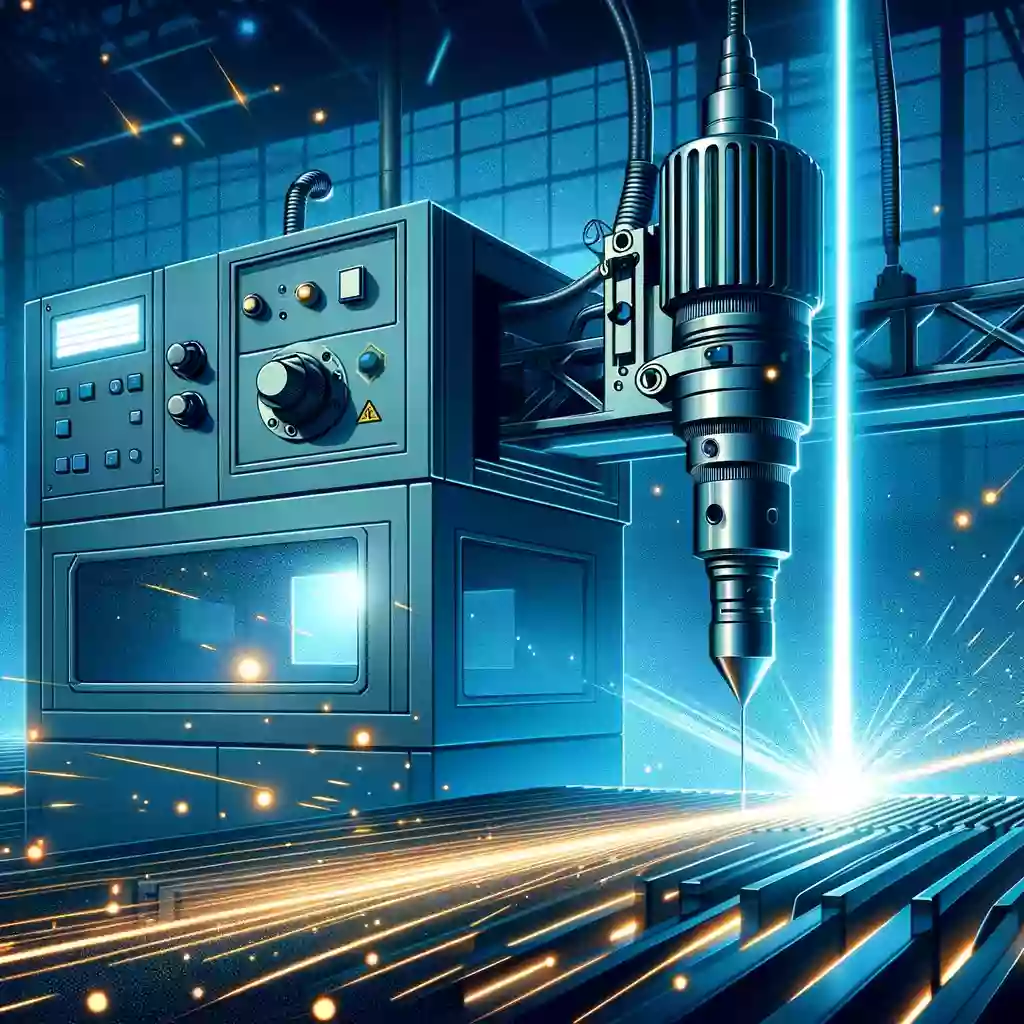
2.Nanoseconds can remove coatings
Nanoseconds enable precise coating removal without damaging or slightly damaging the base material. Since the thickness of the coating is usually much smaller than the width of the ablation, heat cannot be conducted along the sides.
3.Femtosecond laser can cut with precision
Precision laser cutting is one of the common applications of femtosecond lasers, which can be used to cut a variety of substrates.
Final Thoughts
With the continuous advancement of laser technology, the respective advantages of nanosecond, picosecond and femtosecond lasers enable them to play an important role in specific application scenarios. The correct choice of laser type can not only improve production efficiency, but also ensure processing quality and meet the needs of different industries for fine processing. In the future, with the further development and optimization of laser technology, we can expect more innovative applications and broader market prospects.