As an efficient sheet metal processing tool, fiber laser machine has been widely used in various industries. However, many people do not know how to judge the processing quality of metal laser cutting machine when purchasing or using it. So it is difficult to buy high-quality products. The following are some key indicators that can help users evaluate the cutting quality of metal laser cutting machine:
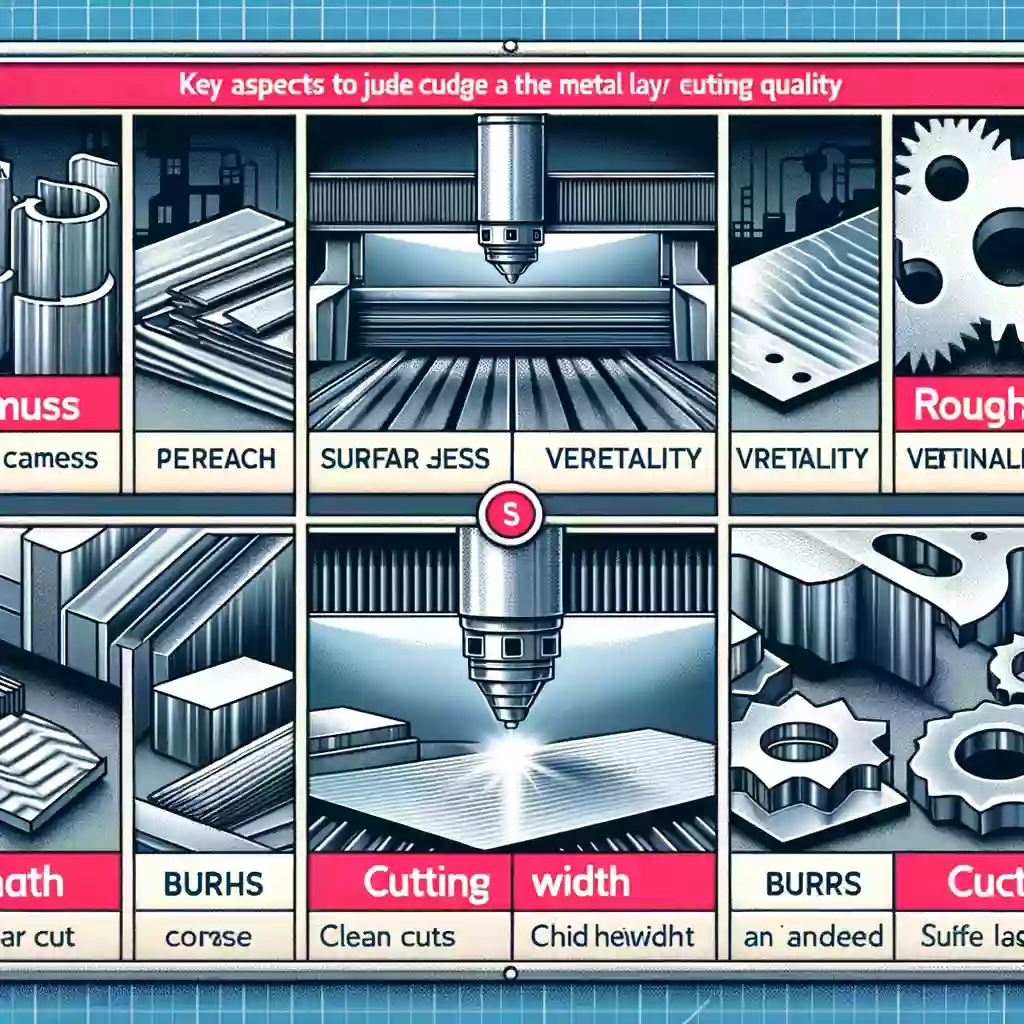
Ⅰ.Roughness
1. Definition of roughness
Fiber laser machine is a high-quality and efficient processing tool. When the laser beam acts on the metal sheet, vertical lines will be formed. The deeper the lines, the rougher the surface of the section. Roughness is one of the important indicators reflecting the microscopic geometric characteristics of the material surface, which directly affects the friction, wear and sealing performance of the parts.
2. Roughness affects the cutting quality and aesthetics
When the cutting machine power matches the thickness of the sheet, the section cut by the metal laser cutting machine should be smooth, without stripes and brittle fracture. Roughness not only affects the appearance of the edge, but also affects the friction characteristics. In most cases, the lower the roughness, the higher the cutting quality. The cutting surface with low roughness is not only beautiful, but also does not require complex processing in the subsequent processing process. Thereby improving production efficiency and reducing costs. Therefore, when evaluating the quality of laser cutting, roughness is an important parameter that cannot be ignored.
Ⅱ.Verticality
1. Definition of verticality
Verticality is one of the important criteria for measuring cutting accuracy, especially for the processing of thick plates. For high-power metal laser cutting, the verticality of the cutting edge is very important when the thickness of the processed material exceeds 10mm. When away from the focus, the laser beam becomes divergent. And the cut may become wider towards the top or bottom depending on the position of the focus. A few hundredths of a millimeter that the cutting edge deviates from the vertical line will affect the overall quality.
2. Verticality affects the processing quality and overall life of the product
If the verticality is not good, it will cause problems when the parts are assembled, affecting the overall quality and service life of the product. Generally, the more vertical the edge, the higher the cutting quality. Therefore, the verticality of the cutting machine when processing thick plates should be tested when purchasing. Therefore, when choosing a laser cutting machine, users should pay special attention to its verticality performance on plates of different thicknesses. And select the best performance equipment through actual testing and comparison of the verticality data of different equipment.
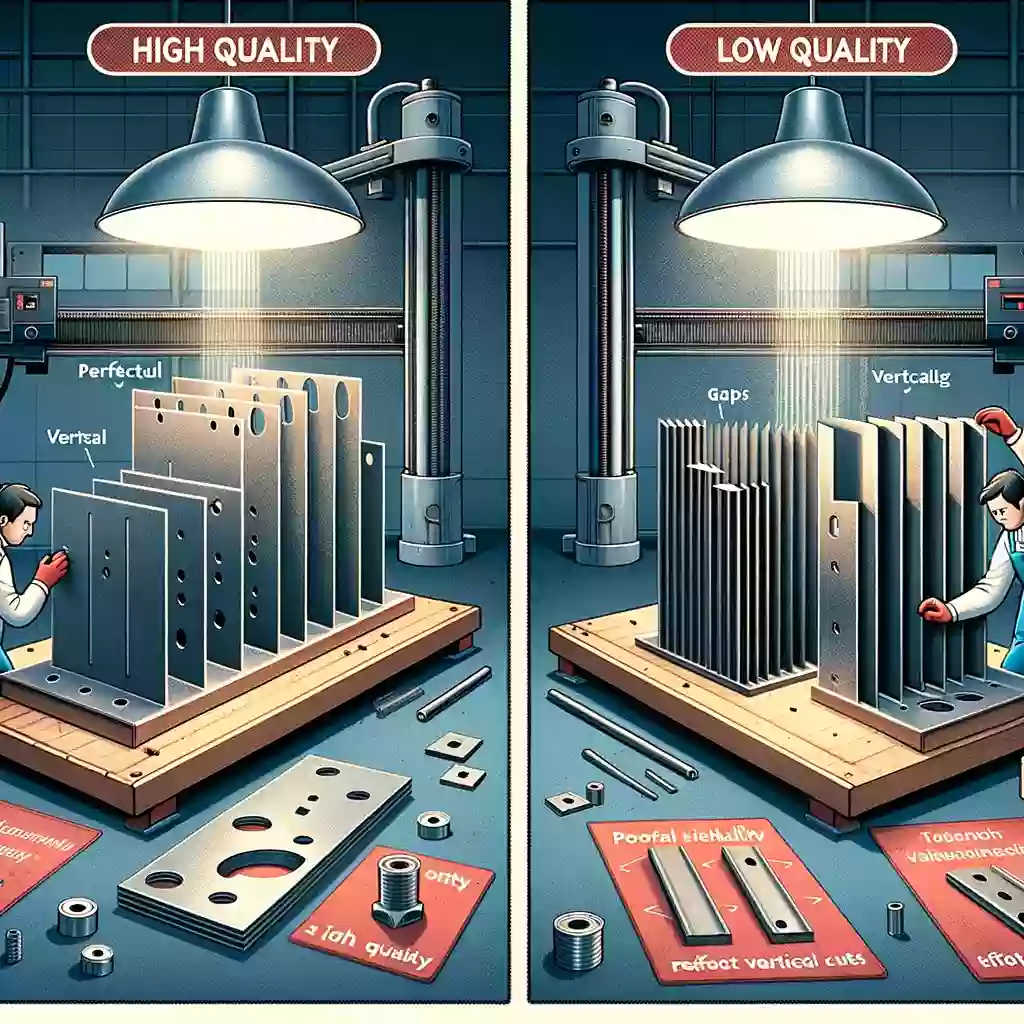
Ⅲ.Cutting width
1. Definition of cutting width
Generally speaking, the cutting width does not directly affect the cutting quality. But when a particularly precise contour needs to be formed, the cutting width determines the minimum inner diameter of the contour. The stability of the cutting width is crucial for the processing of complex contours. When the thickness of the plate increases, the cutting width will also increase. In order to ensure high precision, no matter how large the incision width is. The workpiece should remain constant in the processing area of the laser cutting machine.
2. Cutting width affects complex processing
The stability of the cutting width is crucial for the processing of complex contours. If the cutting width is unstable, it will lead to inaccurate part dimensions, which will affect assembly accuracy and product quality. Especially in industries that require high precision such as aerospace and precision instruments, the control of cutting width is particularly important. Therefore, when choosing a laser cutting machine, priority should be given to those devices with good cutting width stability.
Ⅳ.Burrs
1. Definition of burrs
During the processing of metal laser cutting machines, the high energy generated by the laser beam irradiating the surface of the workpiece will cause the surface of the workpiece to vaporize rapidly and evaporate, and the auxiliary gas will blow off the slag on the surface of the workpiece. If auxiliary gas is not used, burrs will form on the cutting surface after the slag cools. The removal of burrs requires additional work, so the quality of cutting can be intuitively judged by observing the number of burrs. High-quality laser cutting should minimize the formation of burrs.
2. Burrs affect the aesthetics of cutting and subsequent workload
Burrs not only affect the aesthetics of the cut surface, but also increase the workload of subsequent processing. If there are too many burrs, secondary processing such as grinding and polishing may be required, which not only increases the time cost, but also may affect production efficiency. Therefore, when evaluating the quality of the laser cutting machine, the burrs on the cut surface should be observed, and those with less cutting burrs and good surface quality should be selected.
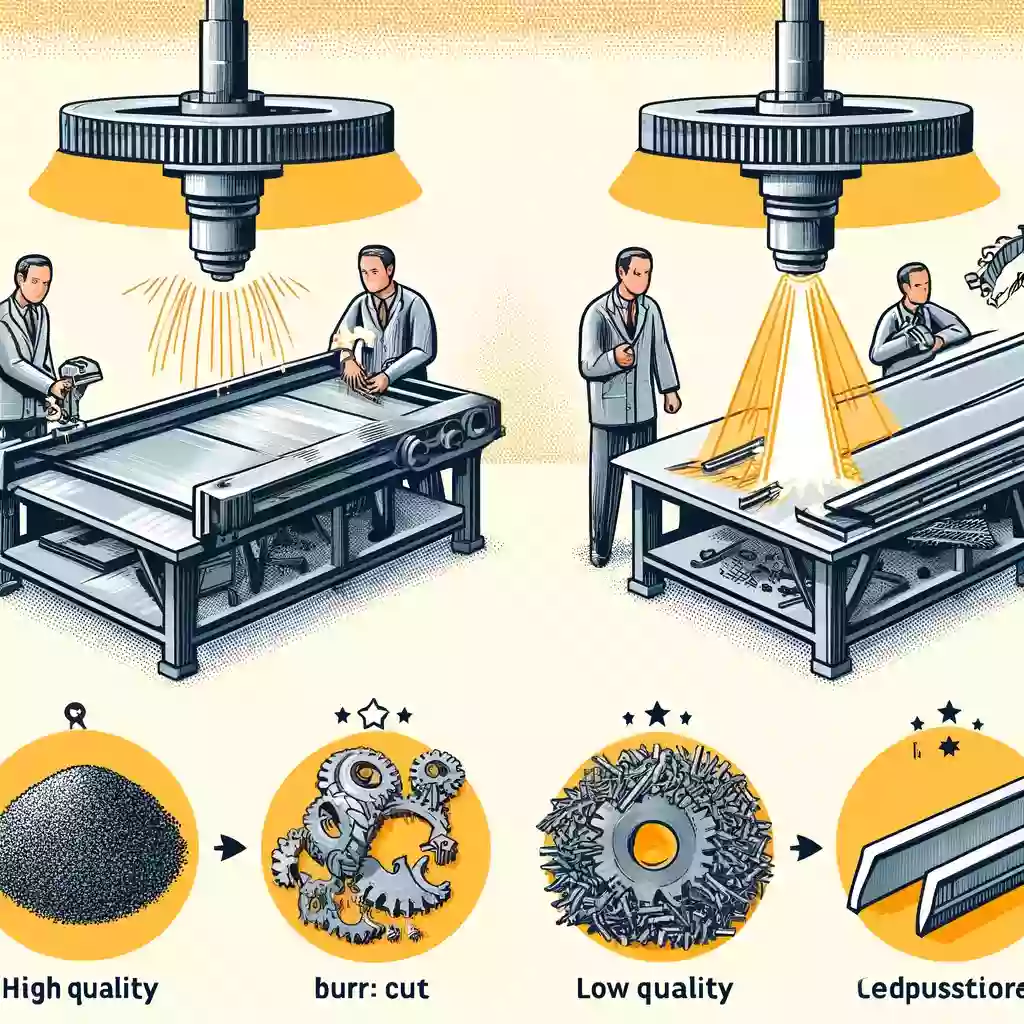
Final Thoughts
When purchasing a metal laser cutting machine, users should comprehensively consider the key indicators of roughness, verticality, cutting width and burrs. By comprehensively evaluating these indicators, the processing quality of the laser cutting machine can be better judged, so as to purchase equipment with excellent performance and suitable for their own needs. In addition, users should also pay attention to the brand reputation, after-sales service and technical support of the cutting machine to ensure that the purchased equipment can maintain stable and efficient operation during use.