As summer approaches, so does the intense heat. While we need to take precautions to prevent ourselves from overheating, it is equally important to pay special attention to the maintenance of our equipment, especially fiber laser machines. In high-temperature environments, if laser cutting machines are not properly maintained, they are prone to malfunctions or even shutdowns. It can affect production efficiency. This article will detail effective maintenance measures to prevent laser cutting machines from “overheating” in the summer. This ensuring that they can continue to operate stably and efficiently in high-temperature conditions.
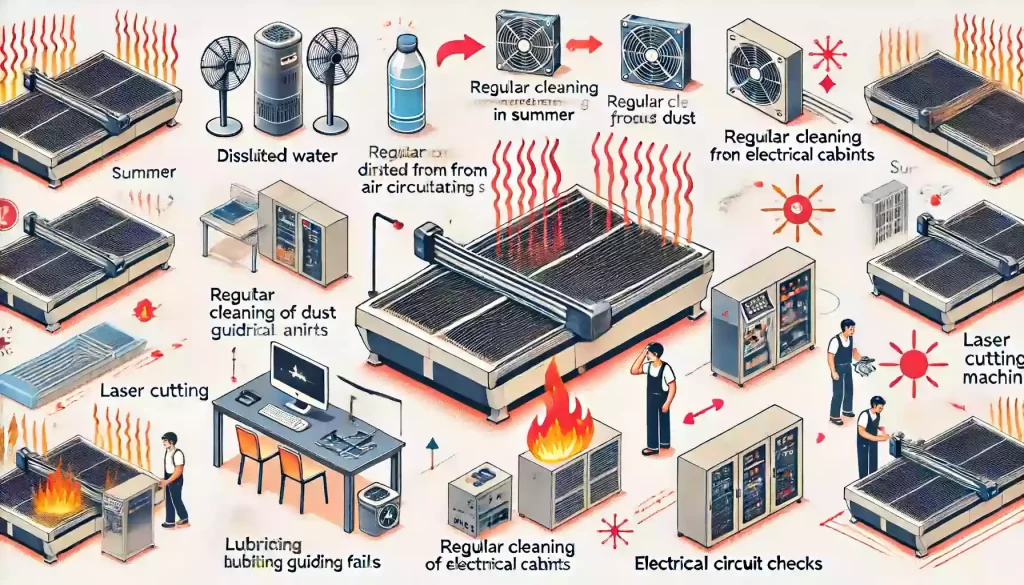
Ⅰ. Cooling
1.Reason:
Fiber laser machines generate a significant amount of heat during operation. And poor cooling is one of the main causes of equipment failure.
2.Measures:
The dust produced by laser cutting primarily consists of particles from the cut grooves that are dispersed into the air. It is advisable to keep the equipment in a well-ventilated environment. Regularly clean the dust from the electrical cabinets and check the operation of cooling fans. This ensure that the cooling system is functioning properly. Additionally, installing fans or air circulation systems in the work area can help the equipment dissipate heat more effectively.
Ⅱ. Water Cooling
1.Cooling water deterioration
In high-temperature weather, the deterioration speed of cooling water increases. It is recommended that users of laser cutting machines use standard distilled or purified water. And regularly clean the scale to prevent it from affecting the laser power due to scale build-up in the laser and pipes.
2.Temperature between cooling water and ambient temperature
The temperature of the cooling water should not differ too much from the ambient temperature. It is recommended to set the water temperature between 25-32 degrees Celsius. As summer temperatures rise, the pressure on the cooling system of laser cutting machines will increase significantly. Therefore, it is advisable to check and maintain the internal pressure of the cooling system before the onset of high temperatures, making timely adjustments to adapt to the hot weather.
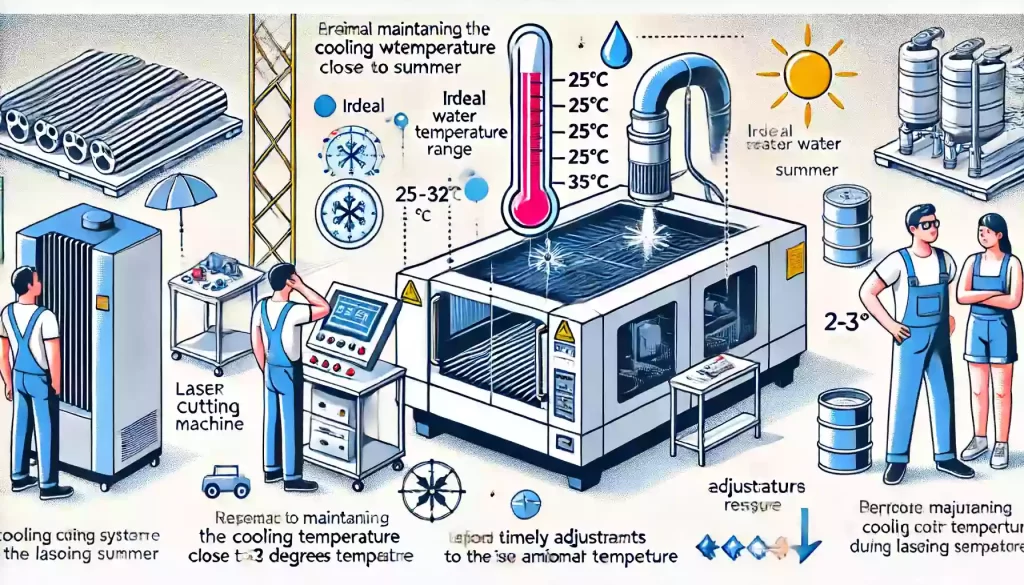
Ⅲ. Lubrication
1.Frequent cleaning
The guide rails of laser cutting machines should be cleaned frequently to remove dust and other debris. This ensuring the normal operation of the equipment. The racks should be wiped regularly and lubricated. In summer, due to higher temperatures, the evaporation rate of lubricating oil increases. Therefore, the lubrication cycle should be shortened by 0.5-1 times compared to spring and autumn. And the oil quality should be monitored.
2.Increase viscosity grade of the lubricating oil
For machinery operating in high-temperature areas, it is appropriate to increase the viscosity grade of the lubricating oil. For oils susceptible to temperature changes, it is essential to add oil appropriately to ensure good lubrication without impurities.
3.Inspect the straightness
Additionally, carefully inspect the straightness of the cutting table tracks and the verticality of the machine, and conduct timely maintenance and adjustments if abnormalities are found.
Ⅳ. Electrical Circuits
1.Reason
In high-temperature environments, wires, plugs, hoses, etc., are prone to aging, leading to decreased insulation performance and increased risk of failure.
2.Measures
Regularly check and replace aging wires, plugs, hoses, and connectors. Inspect the connections of electrical components for loose connections, and tighten them promptly to avoid poor contact, which can cause electrical appliances to burn out and signal transmission instability. Ensuring the reliability of the electrical system is crucial in high-temperature environments, and making sure that every contact point firmly secured is key to preventing equipment malfunctions.
Ⅴ. Regular Inspection and Maintenance
In addition to the daily maintenance measures mentioned above, a regular inspection and maintenance plan should established. During the summer, the inspection frequency can increased to ensure that every component is in good condition. Conduct a comprehensive check of the laser cutting machine, including the laser, cooling system, transmission system, and electrical system, to timely identify and address potential issues. Even for equipment that is not frequently used, it should run periodically to prevent problems from long-term inactivity.
Ⅵ. Optimizing the Operating Environment
Improving the operating environment of the laser cutting machine is also crucial. Avoid placing the equipment in direct sunlight and, if possible, construct shading facilities around it to reduce the impact of ambient temperature on the machine. Keep the workshop clean and ventilated to avoid additional burdens from dust and high temperatures. If conditions permit, equip the laser cutting machine with an independent air conditioning system to maintain a constant and suitable temperature.
Ⅶ. Training and Safety Awareness
Finally, enhancing the training and safety awareness of operators is very important. Operators should have basic knowledge of equipment maintenance and be able to identify and handle common faults during daily work. Additionally, strengthen safety training to ensure that operators use and maintain the equipment correctly, avoiding damage and safety incidents caused by improper operation.
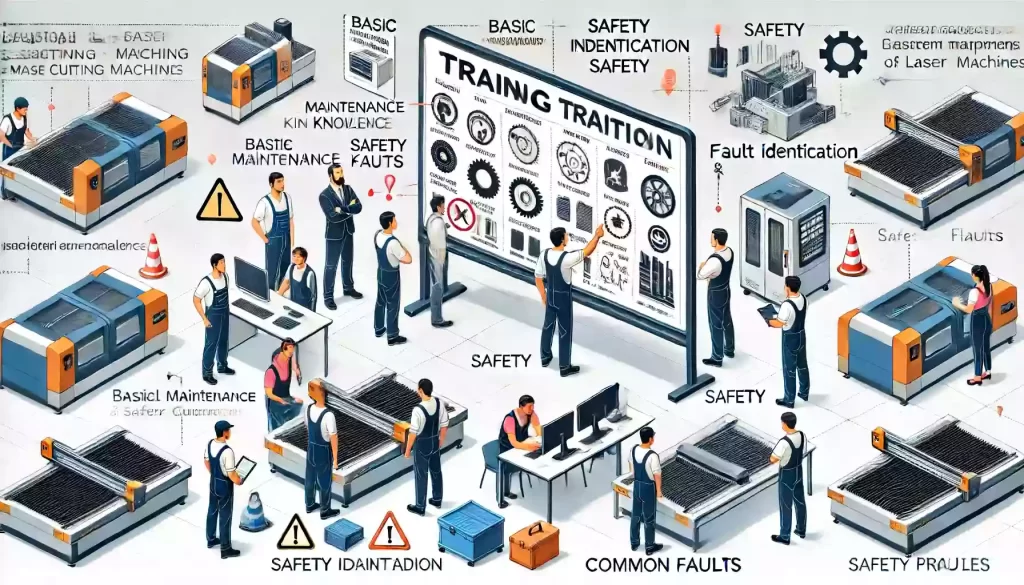
Final Thoughts
By implementing these measures, we can effectively prevent laser cutting machines from “overheating” in high-temperature environments, ensuring their normal operation and improving production efficiency. Regular inspection and maintenance not only extend the equipment’s lifespan but also reduce the failure rate and enhance production safety. We hope that users of laser cutting machines pay attention to summer maintenance to ensure smooth production.