I. Precision in Production
The rise of electronics has brought an unprecedented demand for precision and efficiency in manufacturing processes. Among the myriad of tools available, the metal cutter machine stands out for its critical role in microfabrication. Its importance cannot be overstated, as it plays a pivotal role in producing intricate components essential for modern electronic devices. One standout tool in this realm is the metal laser cutting machine, which excels in delivering the accuracy required in the micro-manufacturing industry.
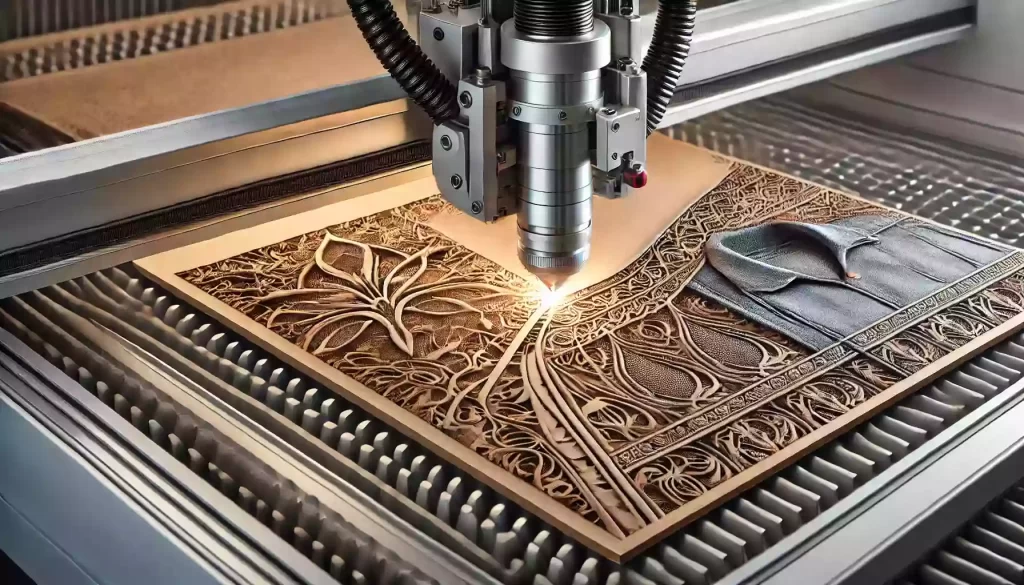
II. Enhancing Accuracy and Reducing Waste
Firstly, the metal laser cutting machine ensures exact cuts that are vital for electronic components. Unlike traditional cutting methods, which often rely on mechanical processes that can introduce variability, this machine utilizes focused laser beams. These beams cut through metal with unparalleled precision, leading to a significant reduction in material waste and enhancing overall material usage. The ability to achieve such accuracy not only conserves resources but also speeds up the manufacturing process—a crucial factor in today’s fast-paced industry where time is often equated with money.
III. Consistency and Error Minimization
In addition to enhancing accuracy, the metal cutter machine also minimizes errors that can occur during production. Manual cutting methods frequently lead to inconsistencies and inaccuracies due to human error and fatigue. In contrast, laser machines provide reliable, consistent results, capable of executing cuts on the smallest features with high precision. They excel at handling complex designs with ease, making them invaluable for producing the advanced electronic components that define modern technology. This reliability translates into fewer defects and reworks, ultimately improving overall production efficiency.
IV. The Shift Towards Automation
Transitioning to another significant benefit, the metal laser cutting machine supports the industry’s shift toward automation. Historically, manual labor was the cornerstone of manufacturing processes; however, the modern landscape is increasingly driven by automation. These machines integrate seamlessly with automated systems, allowing for real-time monitoring and adjustments. This integration boosts productivity, reduces the potential for human error, and ensures consistent quality in every piece produced. The capability to operate within automated frameworks also enhances overall operational efficiency, making it easier to scale production to meet rising demands.
V. Versatility Across Materials
Additionally, the metal cutter machine shines in its versatility. It is capable of cutting a variety of metals commonly used in electronics, including copper, aluminum, and stainless steel. This ability to handle different materials is a game-changer for manufacturers, enabling them to meet diverse demands from clients and markets. Furthermore, the metal laser cutting machine can adjust its power and speed settings for different materials and thicknesses, ensuring optimal performance regardless of the specific requirements. This versatility not only broadens the range of products that can be manufactured but also streamlines the production process, reducing the need for multiple machines.
VI. Ensuring High Repeatability
Moreover, the metal laser cutting machine guarantees high repeatability, a critical factor in micro-manufacturing. In an environment where each component must be identical to the next, maintaining consistency is paramount. Laser cutting machines achieve this by employing sophisticated control systems that ensure each cut meets the exact specifications required. This repeatability is essential for producing reliable electronic devices, as variations in components can lead to malfunctions and increased failure rates in the final products.
VII. Expanding Design Possibilities
The metal cutter machine also enhances design possibilities for manufacturers and designers alike. Traditional cutting methods often impose limitations on creativity, but laser cutting opens up new avenues for innovation. Designers can explore intricate and complex patterns that are essential in modern electronics, including customizable features that cater to specific consumer needs. The metal laser cutting machine enables more innovative designs, allowing companies to differentiate their products in a competitive market, ultimately leading to enhanced consumer satisfaction and brand loyalty.
VIII. Cost Efficiency in Manufacturing
Furthermore, while the initial investment in a metal laser cutting machine may be substantial, the long-term cost efficiencies are noteworthy. These machines significantly minimize waste, lower labor costs, and enhance overall operational efficiency. Over time, the savings achieved through reduced material usage and faster production times can far outweigh the initial capital expenditure. This financial benefit is crucial in a market where cost competitiveness is a constant challenge. Improved efficiency not only leads to faster production times but also positions companies to respond more agilely to market demands and consumer trends.
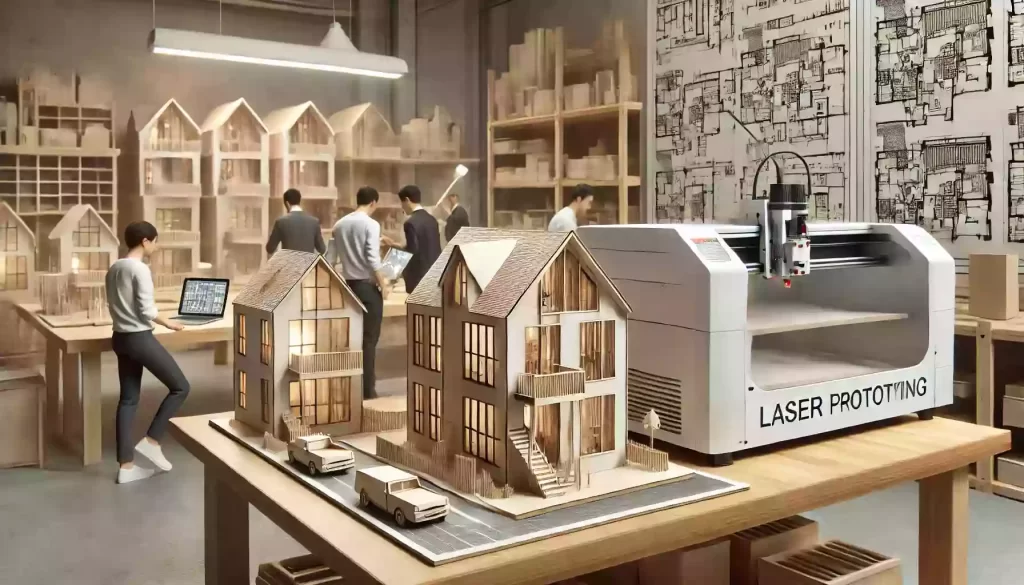
IX. Commitment to Sustainability
In addition to their economic benefits, the metal cutter machine is also more environmentally friendly compared to traditional cutting methods. Conventional cutting techniques often produce significant waste and consume more energy. In contrast, laser cutting is cleaner and more efficient, utilizing less energy and generating minimal waste. This alignment with sustainable manufacturing practices is increasingly important in an era where consumers and regulatory bodies alike are placing greater emphasis on environmental responsibility. The metal laser cutting machine contributes to a greener industry by reducing the overall environmental impact of manufacturing processes.
X. Conclusion
In summary, the metal cutter machine is an indispensable tool in the realm of micro-manufacturing. Its precision, efficiency, and versatility solidify its status as a vital component in the production of electronic devices. The metal laser cutting machine leads the charge in the electronics industry, supporting automation, enhancing design possibilities, and reducing costs. As technology continues to advance and the demand for sophisticated electronic components grows, the role of these machines will only expand. They are indeed the invisible craftsmen in the world of microfabrication, shaping the future of electronics with their unmatched capabilities.