Fiber laser machines are widely used in modern industries due to their high efficiency and precise cutting capabilities. However, for novice operators, ensuring consistent cutting quality can be challenging. When faced with poor cutting quality, the numerous parameters involved can be overwhelming and difficult to adjust correctly. This article provides a detailed overview of the potential issues and corresponding solutions that may arise during the cutting process, aiming to offer practical guidance for beginners.
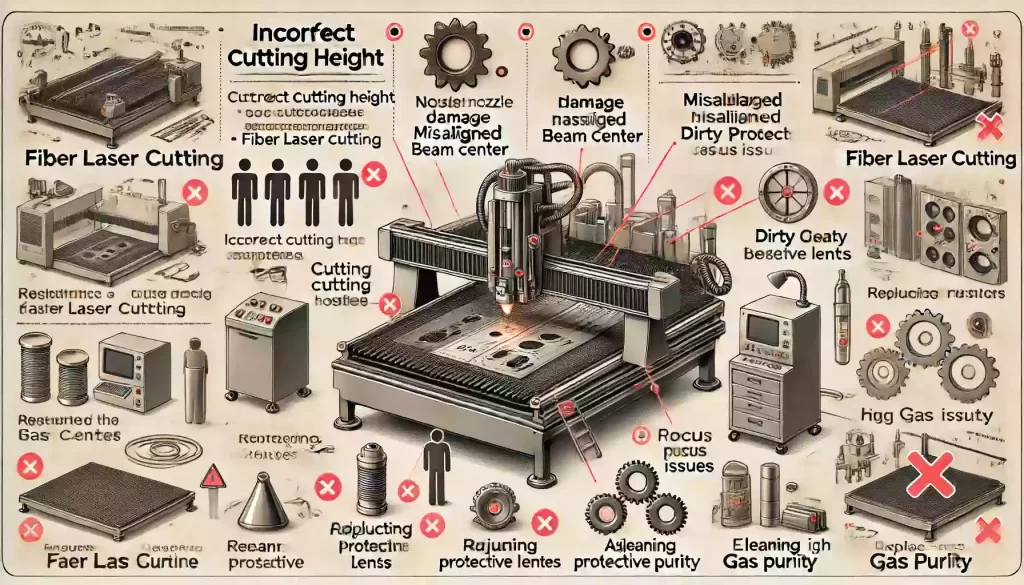
Ⅰ.When encountering poor cutting quality, following steps recommended to first perform a general inspection
The key parameters affecting the cutting quality of fiber laser machines include cutting height, nozzle type, focus position, cutting power, cutting frequency, duty cycle, cutting pressure, and cutting speed. Additionally, hardware conditions such as the cleanliness of protective lenses, gas purity, material quality, focusing lens, and collimator also play a significant role in the cutting outcome.
1.Cutting Height:
The recommended cutting height is between 0.8 to 1.2 mm. If the actual cutting height is inaccurate, recalibration is necessary.
2.Nozzle:
Verify whether the nozzle type and size are correct. Also, check if the nozzle is damaged or if its roundness is normal.
3.Beam Center:
It is suggested to use a nozzle with a diameter of 1.0 mm to check the beam center, with the focal point ideally between -1 and 1. This ensures that the light spot is small and easy to observe.
4.Protective Lens
Check whether the protective lens is clean, with no water, oil, or debris. Weather conditions or cold auxiliary gas can sometimes cause condensation on the protective lens.
5.Focus Position
Ensure that the focus position is set correctly. For automatic focusing cutting heads, use a mobile app to check if the focus is accurate.
6.Adjust Cutting Parameters
After confirming that the above five aspects are in order, adjust the cutting parameters based on the specific issue observed.
Ⅱ.Cutting stainless steel and carbon steel each has its unique characteristics and considerations
1.Stainless Steel Cutting:
If dross is observed on stainless steel cuts, adjust parameters according to the type of dross. For corner dross, consider rounding the corners and adjust parameters such as lowering the focus and increasing the pressure.
For overall hard dross, reduce the focus, increase the pressure, and use a larger nozzle. However, be cautious as too low a focus or too high pressure can lead to layered and rough cut surfaces.
For soft, granular dross, increase the cutting speed or decrease the cutting power.
If dross is observed near the end of the cut, check whether the gas supply is insufficient or if the gas flow is inadequate.
2.Carbon Steel Cutting:
For thin sheets, if the cut surface is not bright, typically a 1000W laser can achieve a bright cut on carbon steel up to 4 mm thick, 2000W up to 6 mm, and 3000W up to 8 mm. To ensure a bright cut surface, the material surface should be free of rust, paint, or oxide scale, and the oxygen purity should be at least 99.5%. Use small nozzles (double-layer 1.0 or 1.2 mm), ensure the cutting speed exceeds 2 m/min, and keep the cutting pressure moderate.
For thick sheets, to achieve good cut surface quality, ensure the material and gas purity, and select the appropriate nozzle. Larger nozzle diameters improve cut surface quality but increase the taper of the cut surface.
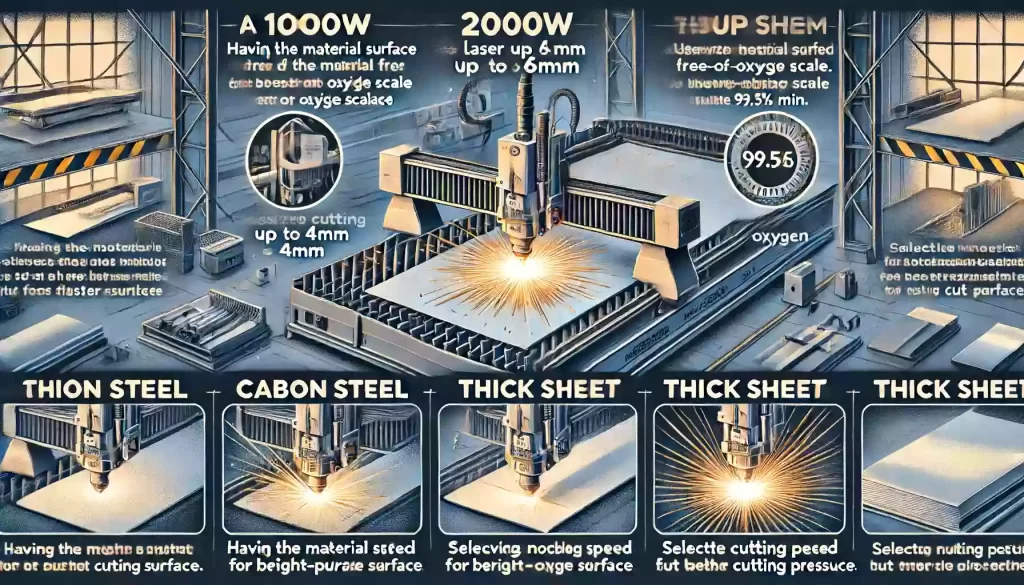
Ⅲ.Common issues and solutions during the cutting process include:
1.Dirty Protective Lens:
A dirty protective lens can reduce laser energy and affect cutting quality. Regular cleaning and replacement of the protective lens are necessary.
Gas Purity: Impure auxiliary gas can impact the cutting effect. Ensure the use of high-purity auxiliary gas.
2.Laser Power Stability:
Unstable laser power output can affect cutting quality. Regular maintenance of the laser to ensure stable output is crucial.
For beginners, familiarizing and mastering these parameters and inspection methods is key to improving cutting quality. Through practical experience, continuous adjustment, and optimization of parameters, cutting results can gradually improve.
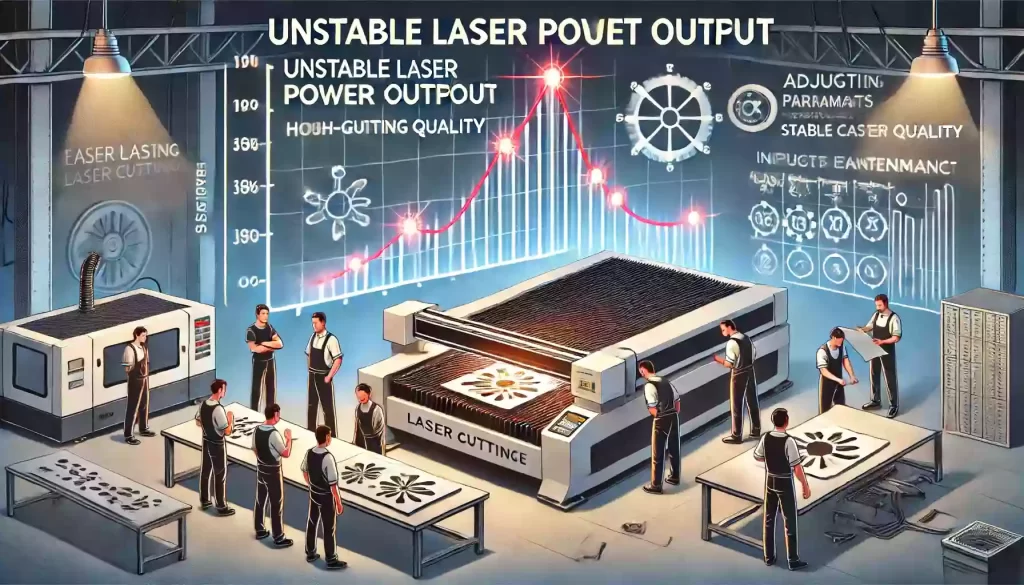
Final Thoughts
In conclusion, the cutting quality of fiber laser cutting machines is influenced by various factors. By accurately adjusting parameters such as cutting height, nozzle type, and focus position, and strictly controlling hardware conditions like protective lens cleanliness and auxiliary gas purity, the cutting quality can be significantly improved. It is hoped that the methods and suggestions provided in this article will help novice operators solve practical problems, improve work efficiency, and achieve high-quality cutting results.