With the rapid development of laser technology, fiber laser machine has increasingly become a crucial tool in various industries. Laser devices, particularly CNC laser cutting machines, have been widely adopted in sectors such as sheet metal, hardware products, steel structures, precision machinery, automotive parts, eyewear, jewelry, nameplates, advertising, crafts, electronics, toys, and packaging. Due to their superior performance and extensive adaptability, CNC laser cutting machines are becoming essential in modern industrial manufacturing.
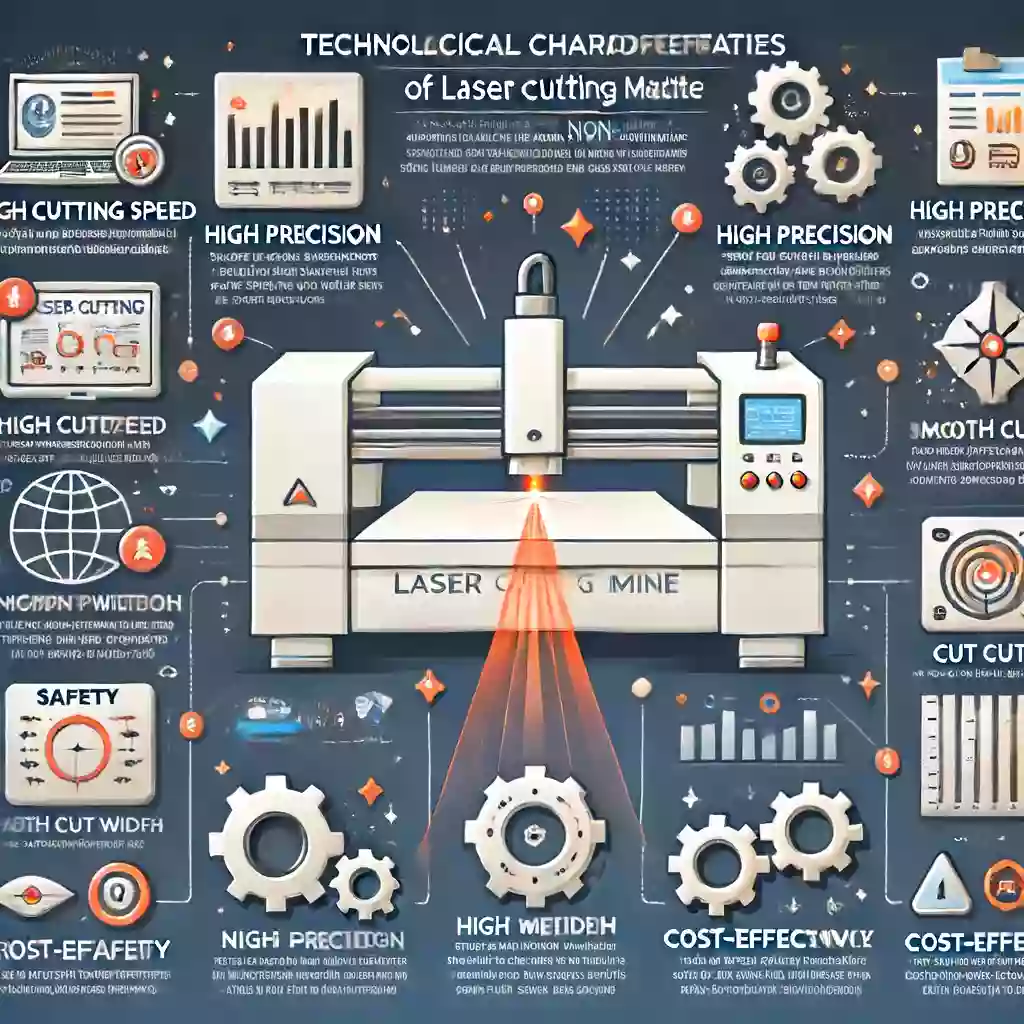
Ⅰ.Significant advantages of CNC laser cutting machines
As laser technology continues to evolve and mature, fiber laser machine has found extensive applications across various fields, such as laser marking machines, laser welding machines, laser drilling machines, and laser cutting machines. Notably, CNC laser cutting machinery has seen rapid development in recent years and is widely used in industries like sheet metal, hardware products, steel structures, precision machinery, automotive parts, eyewear, jewelry, nameplates, advertising, crafts, electronics, toys, and packaging.
1.High Cutting Speed, Quality, and Precision:
CNC laser cutting machines operate at exceptionally high speeds, enhancing production efficiency. Moreover, they deliver excellent cutting quality with smooth edges and high precision, meeting the stringent requirements of various applications.
2.Narrow Cut Width, Smooth Cutting Surface, No Workpiece Damage:
The high precision of laser cutting results in very narrow cut widths, reducing material waste. The cutting surface is smooth, eliminating the need for secondary processing and directly transitioning to the next production stage, significantly saving time and costs.
3.Unaffected by Workpiece Shape or Material Hardness:
Laser cutting machines offer remarkable flexibility, handling complex workpiece shapes with ease. They can process materials of varying hardness, from metals to non-metals, without compromising performance.
4.Capability to Process Both Metal and Non-Metal Materials:
CNC laser cutting machines can cut a wide range of materials, including plastics and wood, extending their application scope significantly.
5.Cost Savings on Molds, Material Conservation, and Overall Cost Reduction:
Unlike traditional cutting methods that require specific molds, laser cutting eliminates the need for molds, significantly reducing mold investment. The high precision of laser cutting also improves material utilization, further lowering production costs.
6.Simple Operation, Safety, Stability, Accelerated Product Development, and Broad Adaptability:
Laser cutting machines feature user-friendly interfaces, high safety, stable performance, and easy maintenance. Their efficient processing capabilities support rapid new product development.
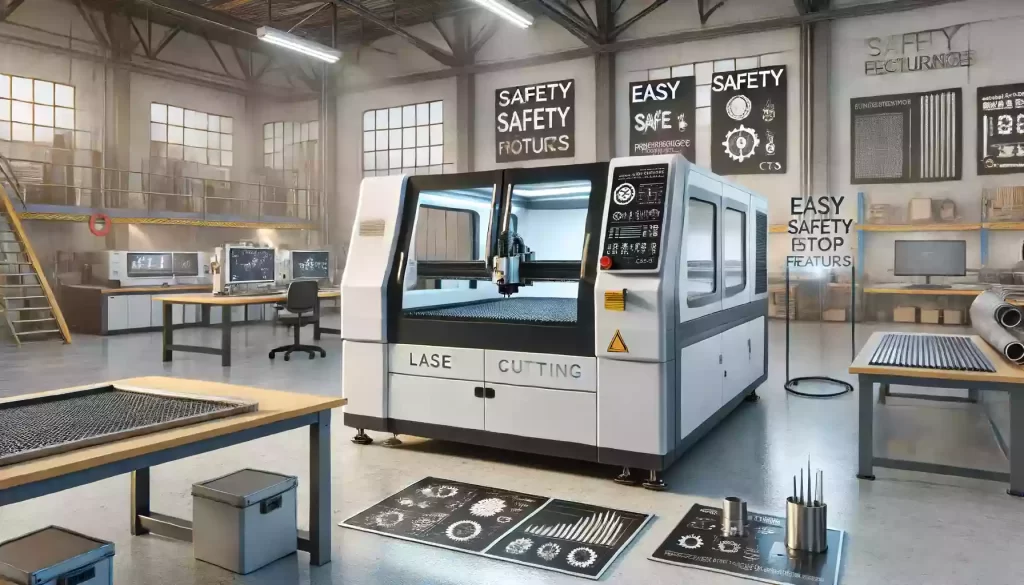
Ⅱ.The design and development of CNC metal laser cutting machine frames
The frame of CNC metal laser cutting equipment is the most crucial component, supporting the majority of parts and bearing the full inertial impact loads during acceleration and deceleration.
1.Determining Conditions for Fast, High-Precision, and Stable Operation Under Various Working Conditions:
Designers need to analyze how different working conditions affect equipment performance to ensure stability and efficiency in diverse environments.
2.Defining Structural Parameters Based on Functional Requirements and Establishing Dynamic Models:
The design process must consider structural characteristics and functional requirements, creating precise dynamic models to optimize the frame design.
3.Studying the Impact of Structure and Parameters on Static and Dynamic Rigidity and Thermal Stability, Providing Theoretical Basis for Frame Design:
In-depth research on how structural parameters affect performance helps formulate scientific design plans, ensuring the frame has good static and dynamic rigidity and thermal stability.
4.Determining the Coupling Relationships Between the Frame and Other Components:
The design process also needs to consider the coupling relationships between the frame and other components to ensure coordinated operation and enhance overall performance.
Ⅲ.Optocouplers have three main features:
1.Signal Transmission in an Electric-Light-Electric Form, Preventing Feedback and Interference:
This transmission method effectively prevents interference and feedback issues during signal transmission, ensuring accurate signal delivery.
2.Strong Noise Suppression Capability:
Optocouplers have strong noise suppression capabilities, effectively reducing the impact of noise on system performance and enhancing stability.
3.Durability, High Reliability, and Fast Speed, with Response Times Generally Within Milliseconds, Some High-Speed Optocouplers Respond in Less Than 10ns:
Optocouplers are highly reliable and durable, with extremely fast response times suitable for various high-speed signal transmission needs.
Ⅳ.Undesirable outcomes
Despite the evident advantages of laser cutting technology, achieving ideal cutting results requires mastering the processing parameters and operating procedures. Specifically, in metal laser cutting processes, selecting the appropriate cutting speed is crucial; otherwise, several undesirable outcomes may occur:
1.If the Cutting Speed is Too Fast, the Following Issues May Arise:
Cutting failure with erratic sparks;
Cut surface showing oblique stripes with melted residues at the bottom;
Rough overall section without melted residues;
2. If the Cutting Speed is Too Slow, the Following Issues May Occur:
Over-melting with a rough cut surface;
Widened cut with complete melting at sharp corners;
Reduced cutting efficiency.
Ⅴ.Judge the cutting speed by observing the cutting sparks:
If the sparks spread from top to bottom, the cutting speed is appropriate.
The second situation:the sparks tilt backward, the feed speed is too fast.
The third situation: if the sparks are not spreading much and are concentrated, the speed is too slow.
Most organic and inorganic materials can be cut with laser cutting machines. Laser cutting technology, compared to traditional cutting methods, has unparalleled advantages. Laser cutting machines not only feature narrow cuts and minimal workpiece deformation but also offer fast speed, high efficiency, low cost, safe operation, and stable performance.
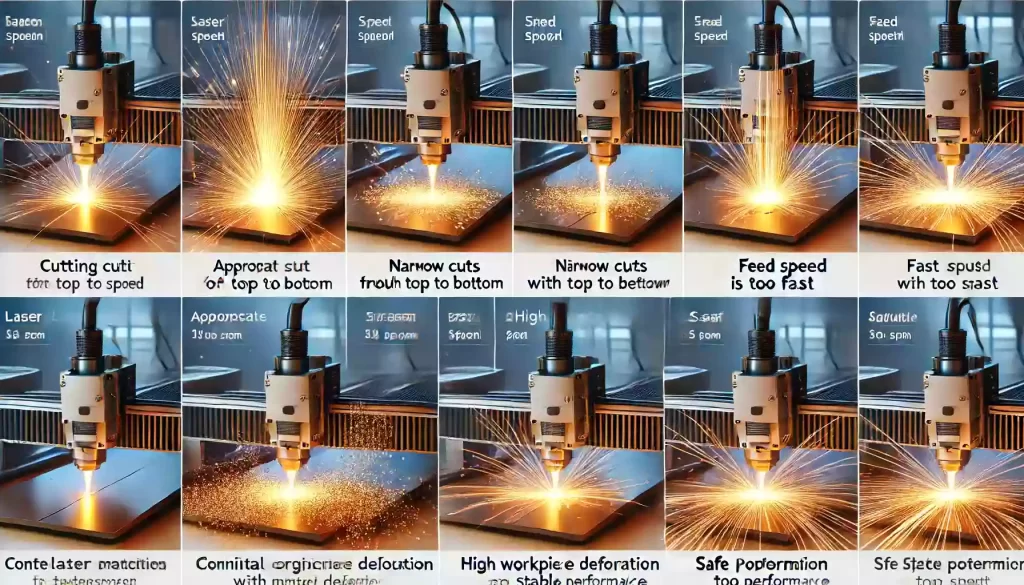
Final Thoughts
In conclusion, laser cutting technology plays a crucial role in modern industrial manufacturing. Its efficiency, precision, and flexibility make it an indispensable tool in various industries. With continuous technological advancements, laser cutting equipment is poised for even broader applications, contributing more significantly to the advancement of industrial automation and intelligent manufacturing.