Laser cutting machines have become indispensable in various industries, especially in the semiconductor sector. The precision, speed, and flexibility of laser cutting make it ideal for working with semiconductor materials. As the demand for smaller and more complex electronic devices grows, the role of laser cutting machines in semiconductor manufacturing becomes even more critical. This article explores how laser cutting machines are applied in the semiconductor industry and their impact on the production process.
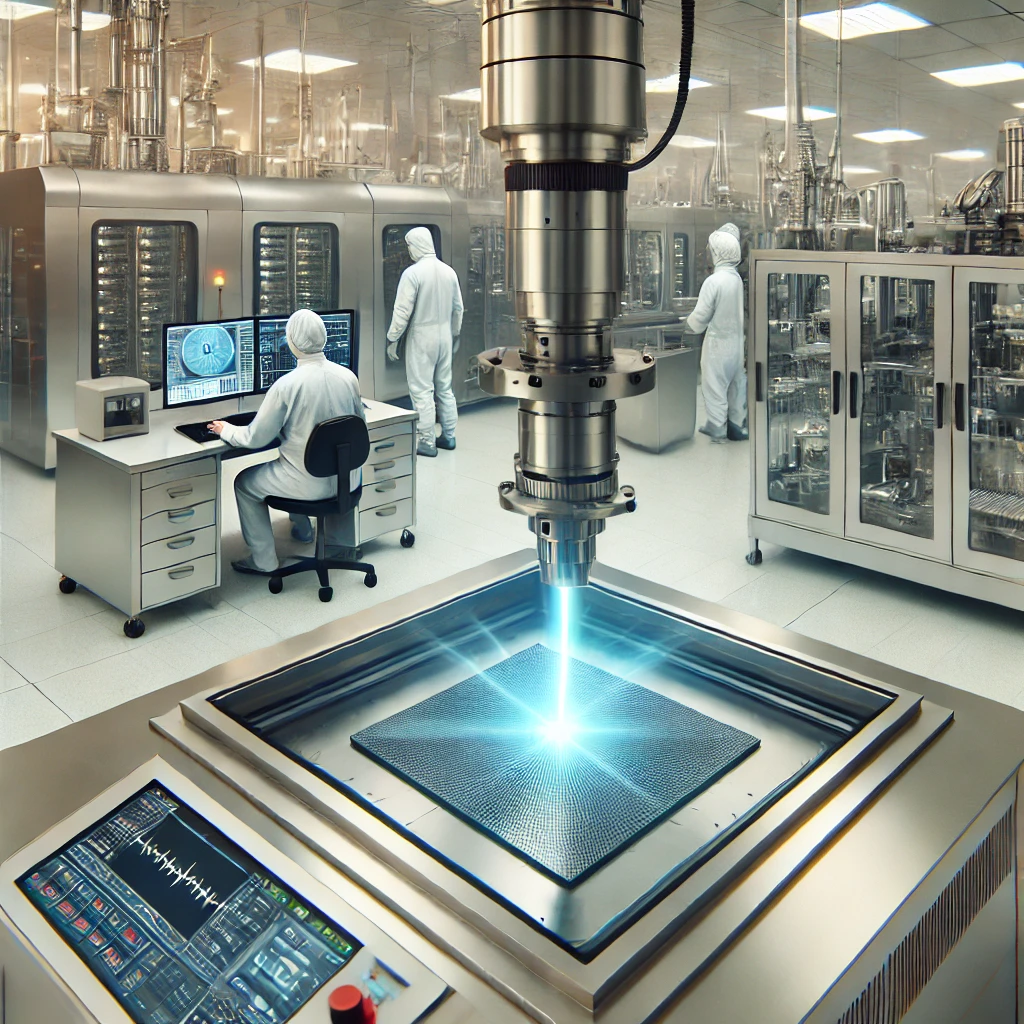
I. Precision and Accuracy in Semiconductor Manufacturing
In semiconductor manufacturing, precision and accuracy are paramount. Semiconductor materials, such as silicon wafers, are delicate and require precise cutting to avoid damage. Laser cutting machines offer the high level of precision needed to handle these materials. The focused laser beam allows for intricate cuts, ensuring that the semiconductor components are accurately shaped and sized. This precision is essential for creating microchips and other semiconductor devices that power modern electronics.
II. Efficiency and Speed
The semiconductor industry operates in a highly competitive environment, where efficiency and speed are crucial. Laser cutting machines are known for their ability to cut through semiconductor materials quickly and efficiently. This speed is particularly important in mass production, where thousands of components must be produced in a short time. Laser cutting machines can complete tasks much faster than traditional methods, reducing production time and increasing output. This efficiency helps manufacturers meet tight deadlines and maintain a competitive edge.
III. Non-Contact Process
One of the significant advantages of using laser cutting machines in semiconductor manufacturing is the non-contact process. The laser beam cuts without physically touching the material, reducing the risk of contamination or damage. This is particularly important in the semiconductor industry, where cleanliness and precision are critical. The non-contact process also means that delicate semiconductor materials can be cut without being deformed or cracked. This ensures the integrity and functionality of the semiconductor components.
IV. Versatility in Material Types
Laser cutting machines are highly versatile and can work with various types of semiconductor materials. These include silicon, gallium arsenide, and other compound semiconductors. This versatility is essential in the semiconductor industry, where different materials are used for different applications. Whether cutting thin silicon wafers or thicker semiconductor substrates, a laser cutting machine can handle a wide range of materials with ease. This versatility allows manufacturers to produce a variety of semiconductor devices with consistent quality.
V. Customization and Flexibility
Laser cutting machines offer high levels of customization and flexibility in semiconductor manufacturing. They can be programmed to create unique designs and patterns on semiconductor materials. This is particularly useful in the production of custom semiconductor devices, such as specialized microchips and sensors. The flexibility of laser cutting machines allows manufacturers to quickly adapt to changing customer demands and produce small or large batches of customized products. This adaptability is crucial in an industry where innovation and rapid development are the norms.
VI. Reduced Material Waste
In semiconductor manufacturing, minimizing material waste is essential for cost efficiency and sustainability. Laser cutting machines are highly efficient in material usage, ensuring precise cuts with minimal waste. The precision of the laser allows for close nesting of components, maximizing the use of the semiconductor material. This reduction in waste is not only cost-effective but also environmentally friendly. In an industry where materials like silicon are valuable, reducing waste through efficient laser cutting is a significant advantage.
VII. Enhanced Cutting Quality
The quality of the cut is critical in semiconductor manufacturing, as any imperfections can affect the performance of the final product. Laser cutting machines produce clean and smooth edges, which are crucial for semiconductor components. Unlike mechanical cutting methods, laser cutting does not cause rough or jagged edges. The laser beam melts the semiconductor material as it cuts, resulting in a polished finish. This high-quality cutting is essential for ensuring that semiconductor devices function correctly and reliably.
VIII. Integration with Automation Systems
The semiconductor industry increasingly relies on automation to improve production efficiency and consistency. Laser cutting machines can be easily integrated into automated production lines, enhancing their capabilities. Automation systems can control the laser cutting process, ensuring consistent quality and reducing the risk of human error. This integration also allows for real-time monitoring and adjustments, further improving the precision and efficiency of the cutting process. The combination of laser cutting and automation is driving innovation in semiconductor manufacturing.
IX. Challenges and Solutions
Despite the many advantages, there are challenges associated with using laser cutting machines in semiconductor materials. One challenge is managing the heat generated by the laser, which can affect the semiconductor material’s properties. However, advances in laser technology have led to the development of cooling systems and optimized cutting parameters that minimize this risk. Another challenge is ensuring the correct laser settings for different semiconductor materials, but with proper calibration, these machines can be adjusted to handle various materials effectively.
X. Future Prospects
The future of laser cutting machines in semiconductor manufacturing looks promising. As technology continues to advance, these machines will become even more precise and versatile. The development of new semiconductor materials and devices will drive further innovation in laser cutting technology. Additionally, as laser cutting machines become more accessible, their use in semiconductor manufacturing will likely expand, leading to more widespread and effective production processes.
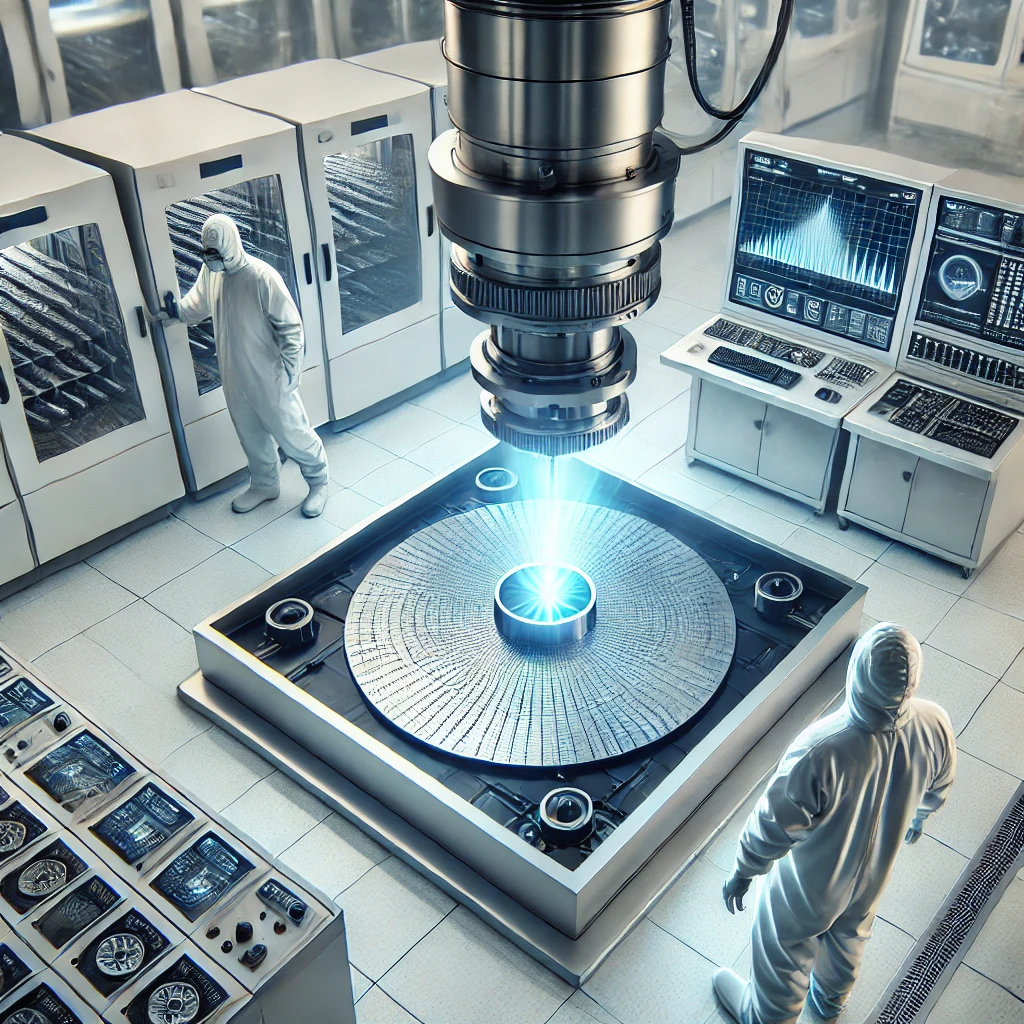
XI. Conclusion
Laser cutting machines have revolutionized the semiconductor industry by offering precision, efficiency, and versatility. Their application in cutting, shaping, and engraving semiconductor materials has made them indispensable tools in the production of microchips and other semiconductor devices. As technology continues to evolve, the role of laser cutting machines in semiconductor manufacturing will only grow, driving innovation and improving production efficiency. With the right approach, laser cutting machines will continue to play a crucial role in the future of semiconductor manufacturing.