Shipbuilding is a complex and demanding industry. It requires precision, efficiency, and innovation. The introduction of laser cutting machines has revolutionized the shipbuilding process. These machines offer unparalleled accuracy and speed, making them essential tools in modern ship construction. The integration of laser cut machining into shipbuilding has improved both the quality and efficiency of production, leading to more durable and reliable vessels.
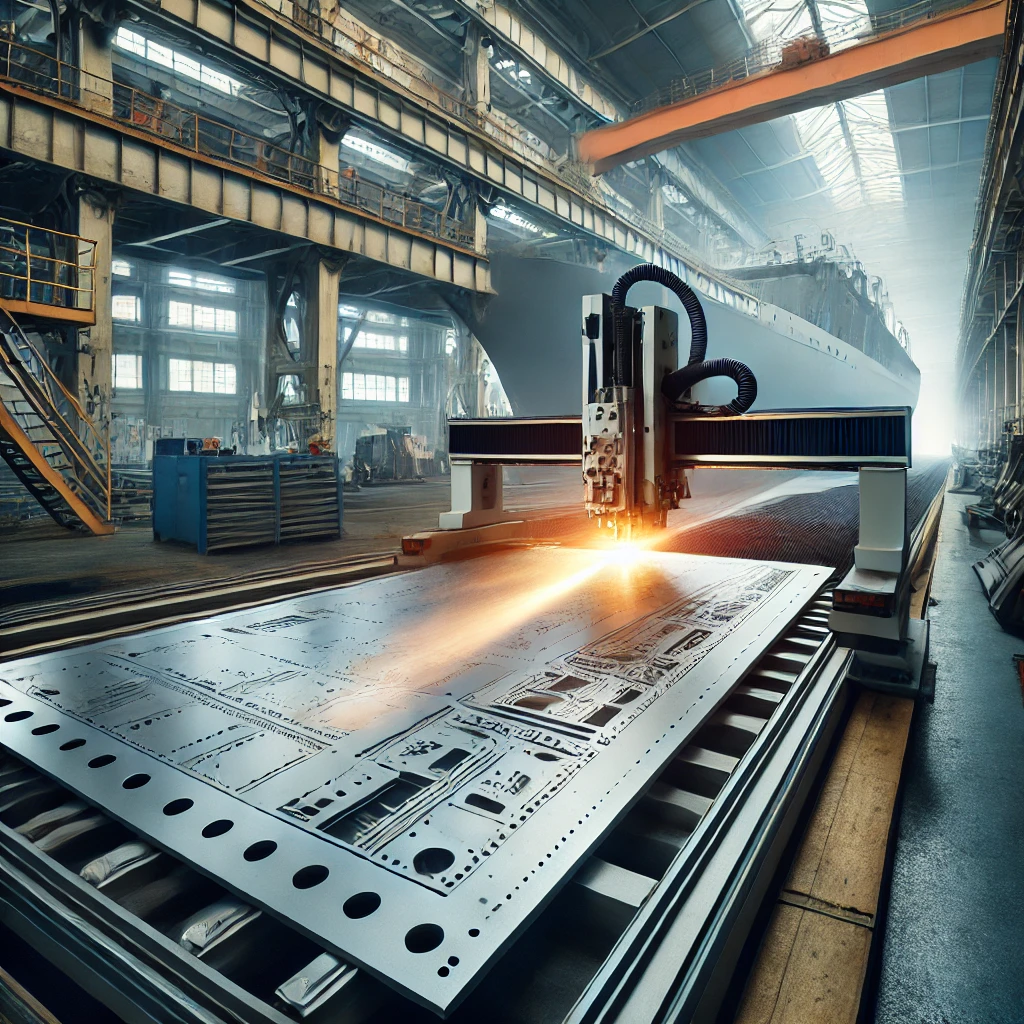
I. Enhancing Precision in Shipbuilding
Shipbuilding demands high levels of precision. Every component must fit perfectly to ensure the vessel’s structural integrity. Laser cutting machines provide this precision by using focused laser beams to cut materials with extreme accuracy. The laser’s precision ensures that each piece is cut to exact specifications, reducing the need for adjustments during assembly.
Moreover, laser cut machining allows for the creation of complex shapes and intricate designs. This capability is particularly important in shipbuilding, where components often have unique and challenging geometries. The laser’s ability to cut through various materials, including steel and aluminum, ensures that all parts meet the highest standards of quality.
II. Improving Efficiency and Speed
Speed is crucial in shipbuilding. Traditional cutting methods are often time-consuming and labor-intensive. Laser cutting machines significantly improve production speed by automating the cutting process. Unlike traditional methods, which may require multiple steps, laser cut machining completes the task in one pass. This efficiency reduces production time, allowing shipbuilders to meet tight deadlines.
Furthermore, the laser’s ability to cut through thick materials quickly without compromising precision is a significant advantage. This capability is particularly beneficial in shipbuilding, where large metal sheets are often used. By reducing cutting time, laser cutting machines help shipyards increase productivity and reduce costs.
III. Reducing Material Waste
Material waste is a major concern in shipbuilding. The high cost of materials like steel and aluminum makes waste reduction essential. Laser cutting machines help minimize waste by optimizing the cutting process. The precision of laser cut machining ensures that materials are used efficiently, with minimal offcuts or scrap.
Additionally, laser cutting machines can create intricate designs without additional tools, reducing the need for excess material. This optimization not only lowers costs but also contributes to more sustainable shipbuilding practices, which are increasingly important in today’s industry.
IV. Enhancing Structural Integrity
The structural integrity of a ship is paramount. Any flaws in the construction process can lead to serious safety issues. Laser cutting machines contribute to the durability and safety of ships by producing high-quality, precise parts. The clean cuts made by the laser reduce the risk of stress points, which can lead to cracks or failure under pressure.
Moreover, laser cut machining can be used to create components with reinforced edges or specific surface textures that enhance their durability. These features are particularly important for parts exposed to harsh marine environments, where corrosion and wear are significant concerns.
V. Facilitating Complex Design Implementation
Modern shipbuilding often involves complex and innovative designs. Laser cutting machines provide the flexibility needed to implement these designs effectively. Whether it’s a unique hull shape or an intricate internal structure, laser cut machining can accommodate these requirements with ease. The laser’s precision ensures that even the most complex designs are executed flawlessly.
Furthermore, laser cutting machines allow for rapid prototyping. Shipbuilders can quickly create and test components before full-scale production begins. This capability is particularly useful for custom or experimental designs, where adjustments may be needed based on initial tests.
VI. Supporting Innovation in Shipbuilding
Innovation is key to the advancement of shipbuilding technology. Laser cutting machines play a vital role in supporting this innovation. By enabling the creation of complex and precise components, laser cut machining allows designers and engineers to push the boundaries of what is possible in ship construction.
For example, laser cutting machines can be used to create lightweight yet strong components that improve a ship’s efficiency. This innovation leads to the development of more advanced vessels that can perform tasks more effectively, reduce fuel consumption, and minimize environmental impact.
VII. Enhancing Safety and Compliance
Safety is a top priority in shipbuilding. Laser cutting machines contribute to safer vessels by ensuring that all components are made with precision and consistency. Laser cut machining reduces the likelihood of defects that could compromise the safety of the ship.
Additionally, laser cutting machines help shipbuilders meet strict industry standards and regulations. The precision of the laser ensures that all parts comply with safety requirements, reducing the risk of accidents and ensuring the reliability of the vessel.
VIII. The Future of Laser Cutting in Shipbuilding
As technology continues to evolve, the role of laser cutting machines in shipbuilding will likely expand. Future advancements in laser cut machining may include even greater precision and the ability to work with a wider range of materials. These innovations will further enhance the quality and performance of ships.
Moreover, as laser cutting machines become more accessible and affordable, their use in the shipbuilding industry will likely increase. The ability to make precise, on-site adjustments and repairs will become increasingly valuable, particularly for custom or large-scale shipbuilding projects.
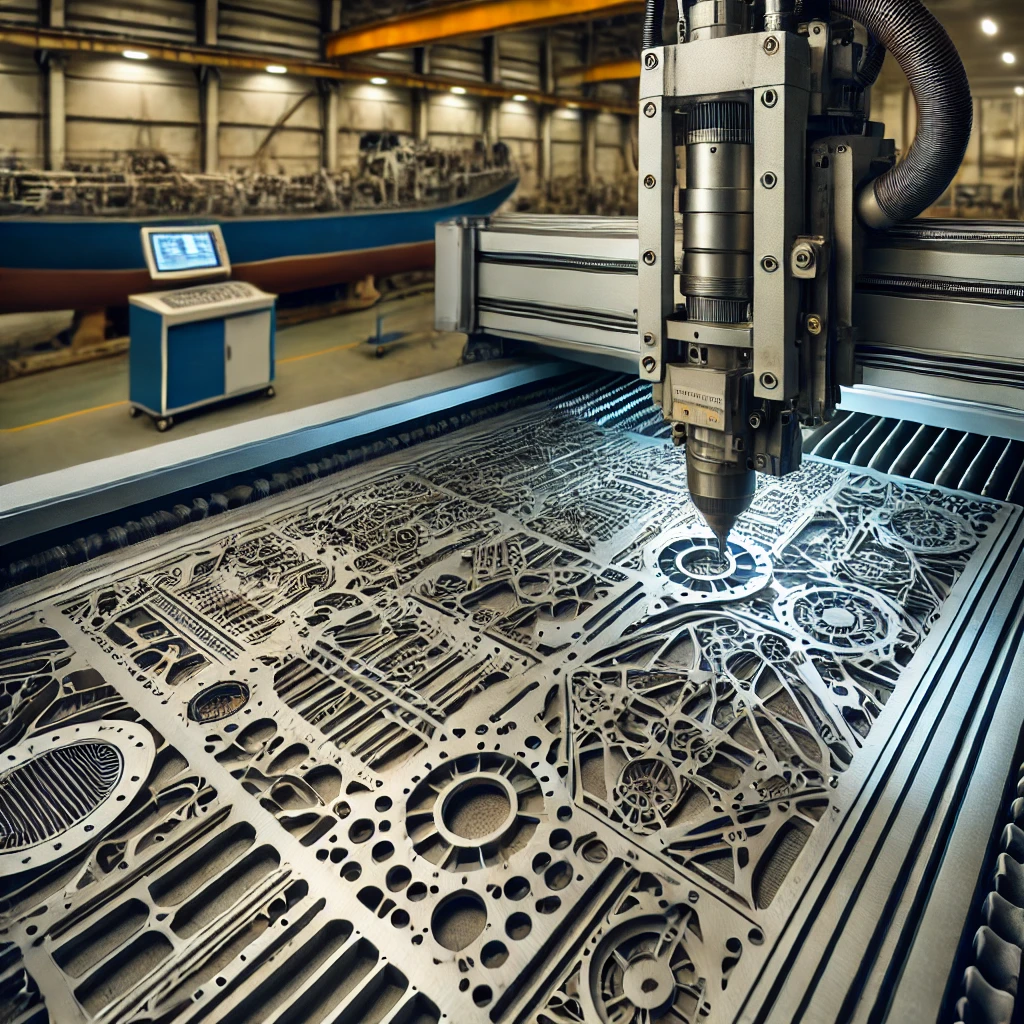
IX. Conclusion
In conclusion, laser cutting machines have revolutionized the shipbuilding industry by providing precision, efficiency, and flexibility. The application of laser cut machining has enhanced the quality and safety of ships, ensuring that they meet the highest standards. As the industry continues to evolve, laser cutting machines will remain at the forefront, driving innovation and improving the performance of vessels. The future of shipbuilding will undoubtedly be shaped by the continued advancement and application of laser cutting technology.