Laser cutting machines, with their exceptional ability to cut through diverse materials from metals to organics, are indispensable in many industries. Nonetheless, their accuracy relies largely on regular and meticulous maintenance. This detailed blog analyzes the distinct maintenance procedures required for the efficient operation and lifespan extension of a laser cutting machine.
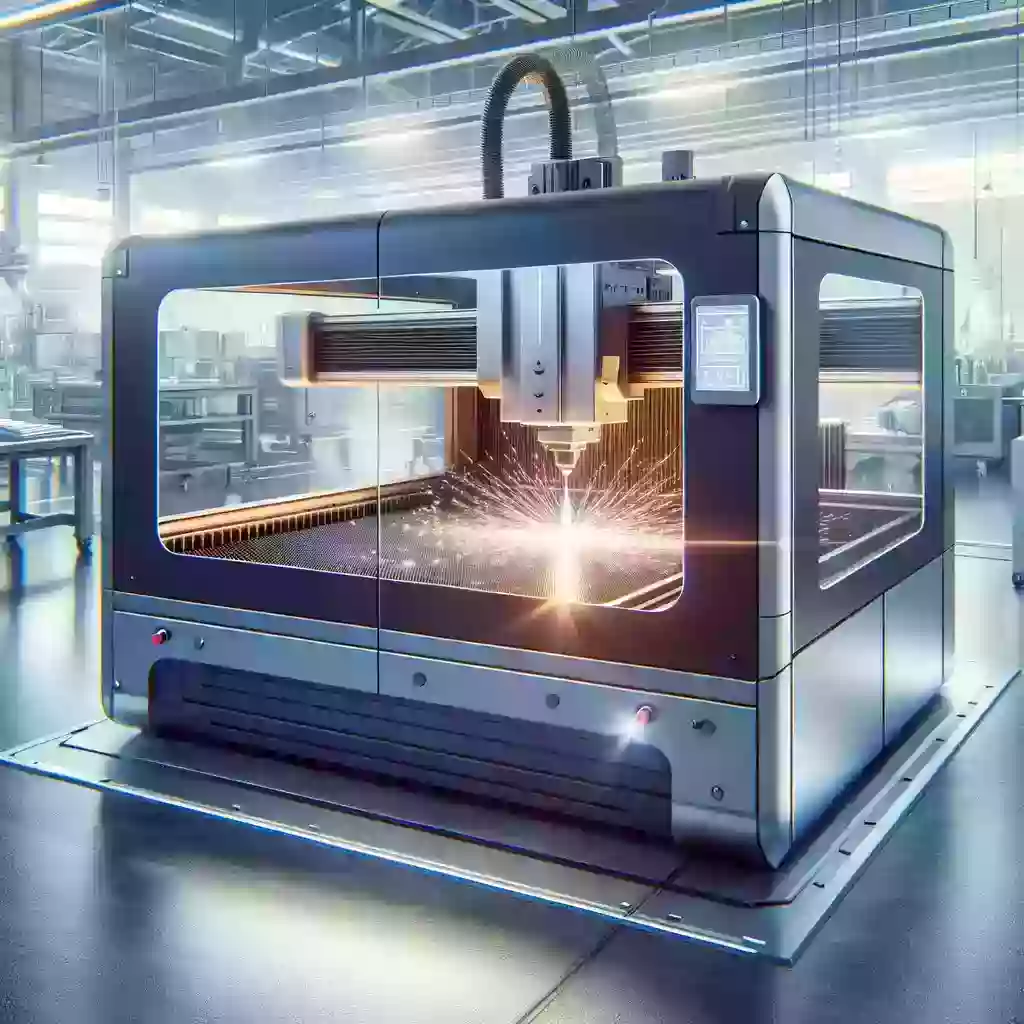
Basic Procedures for Cleansing of Maintenance
The accuracy of a laser machine can be easily undermined by the accumulation of debris such as smoke, dust, and other particles. This makes it very important to regularly clean key parts like the laser lens, the mirrors, and the work area. Ideally, the cleaning frequency should match the frequency of usage or cleaning frequency should be increased in highly polluted environments
1.Lenses and Mirrors:
Vigilantly clean lenses and mirrors with a gentle, lint-free cloth coated in isopropyl alcohol. Steer clear of hands without contact with these parts since skin oils can create remnants that hinder the laser’s trajectory and harm the work efficiency of laser machines.
2.Work Area:
Remove all debris and residues from the cutting area and the exhaust system. Accumulated buildup in exhaust pipes can diminish its efficacy, resulting in inferior air quality and ensuing risks.
Maintaining and Substituting Laser Tube
The beam’s creation is by the laser tube, making it crucial to the laser cutting machine’s operation. Over time, laser tube’s working effectiveness wanes; its power output diminishes, necessitating monitoring for indications of decreased efficiency or inconsistent quality of cutting.
1.Expected Longevity of Tube:
The lifespan of a laser machine, based on its model and the level of use, ranges from 1,000 to 2,000 hours. Regular performance evaluations are beneficial in knowing the need for a replacement.
2.Protocol for Replacement:
The process of changing a laser tube entails recalibration of the laser machine. The task may need expert help, particularly when it comes to high precision laser cutting machines.
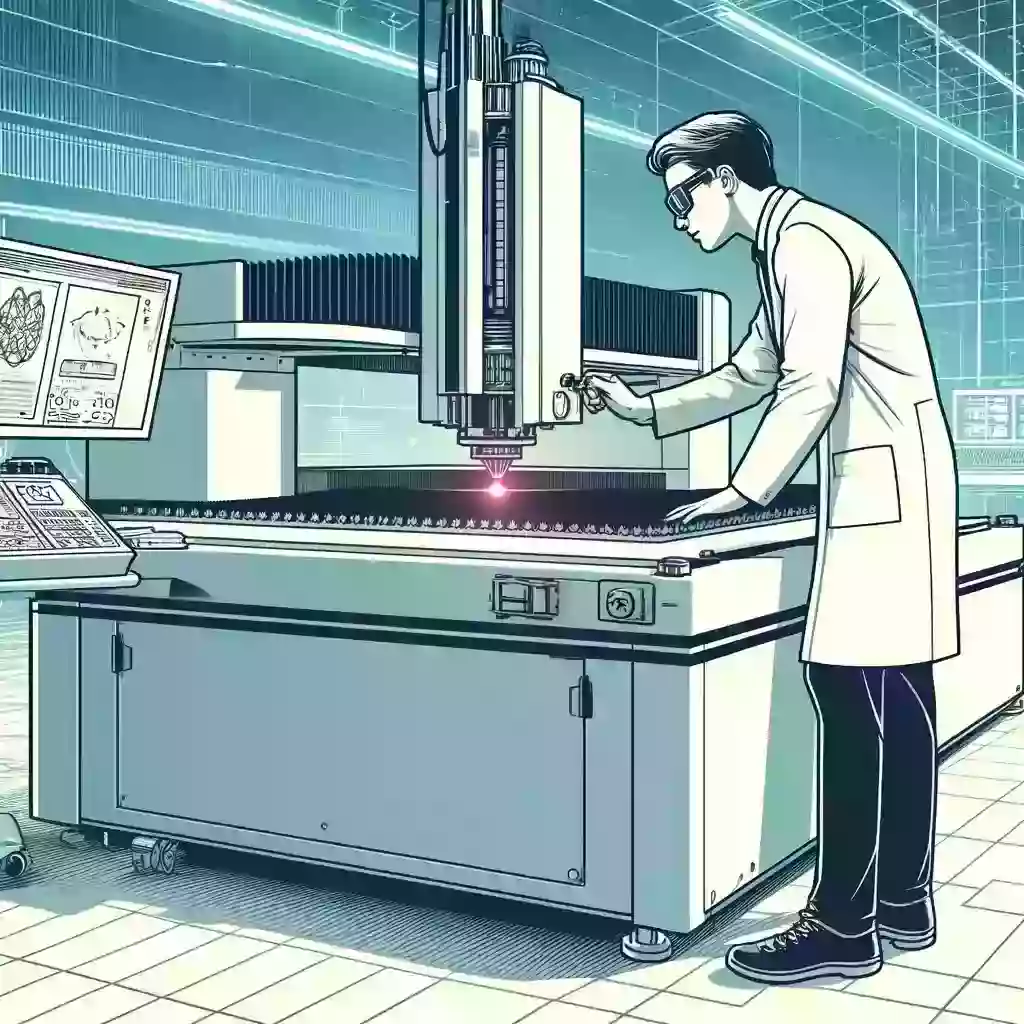
Alignment Checks of Laser Cutting Machine
Laser cutting machine alignment is of utmost significance. Even slight misalignments have the potential to lead to notable variations in the precision of cuts.
1.Frequency:
Ensure laser alignment is verified every three to six months or following potential incidents affecting the laser machine’s physical integrity.
2.Method:
Adjust the mirrors to guarantee the laser beam moves with high precision from the emitter to the desired material. The process here can be intricate and might necessitate the use of distinct alignment instruments.
Upkeep of the Cooling System
Excessive heat may lead to harm in a laser cutting machine. It’s vital to upkeep the cooling system, be it water or air.
1.Water Chillers:
Surveillance of the water’s purity level and water levels. Change the water as per the maker’s advice, opting for distilled water to circumvent mineral buildup.
2.Air Chillers:
Maintain cleanliness and unobstructed ventilation for optimal dissipation of heat.
Lubricating and Mechanical Well-being
Components like belts, gears, and rails guarantee the laser’s exact motion and necessitate regular lubrication for reduced wear.
1.Lubrication Period:
Use a lightweight machine oil every two months or whenever necessary for maintaining smooth functioning.
2.Rear and Wear:
Regularly check laser machine’s moving parts such as belts, gears, and rails for indications of harm or severe deterioration. Swiftly swap out aged components to prevent system malfunctions.
Integrity of Electrical Systems
Ensuring the dependability of a laser cutting machine’s electrical setup is of utmost importance. Dysfunctional wiring or connections may result in in operational inefficiencies or risks to safety.
1.Method:
It’s advised to conduct bi-yearly check-ups to confirm the security of all connections and verify the proper operation of laser cutting machine’s elements such as the power supply. Contemplate employing an expert for these checks.
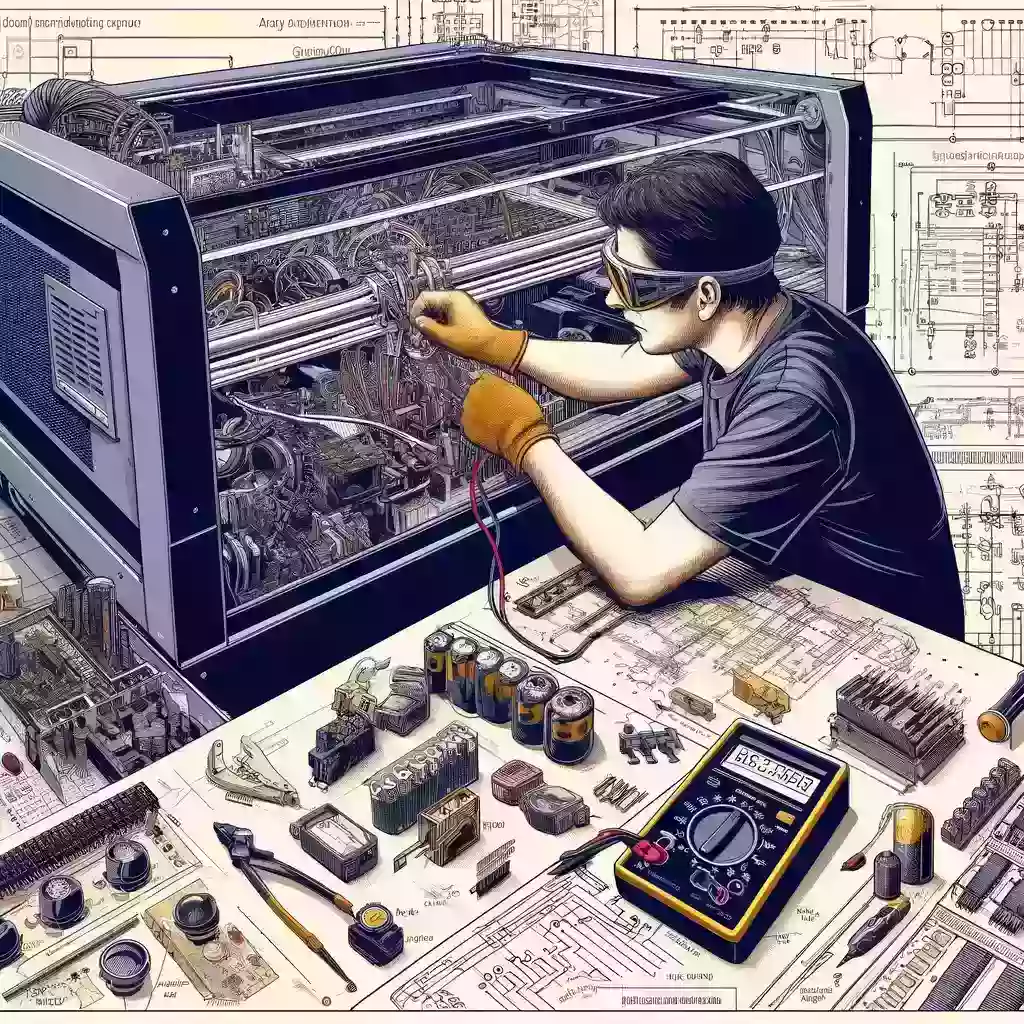
Updates and Calibration of Software
The laser machine’s functionality is regulated by software. The frequent updates of this software guarantee laser cutting machine’s compatibility across various materials and cutting methods.
1.Update:
Install the newest version provided by the manufacturer to improve both performance and security.
2.Calibration:
Regularly recalibrate the software to match the unique features of the cutting materials , modifying parameters such as power, swiftness, and focus.
Professional Service
Annual professional service complements regular upkeep. A skilled technician is proficient in comprehensive assessments of laser machines and undertaking intricate repairs beyond standard servicing, guaranteeing the device functions at maximum efficiency.
Final Thoughts
Regular and meticulous upkeep of laser machines is crucial for preserving its operational accuracy and prolonging its lifespan. Adhering to a strict schedule for maintenance and swiftly dealing with all matters, companies can whole hog utilize their investment in laser machines, guaranteeing uninterrupted high quality cuts and upholding workplace safety .