Laser cutting is a common processing technology used in industrial and creative projects, providing precise and clean cuts. However, not all materials are suitable for processing with a fiber laser machine. Some materials may produce toxic fumes, damage equipment, or cut poorly. In this blog we will look at some materials that are not suitable for laser cutting, and alternative processing methods for these materials.
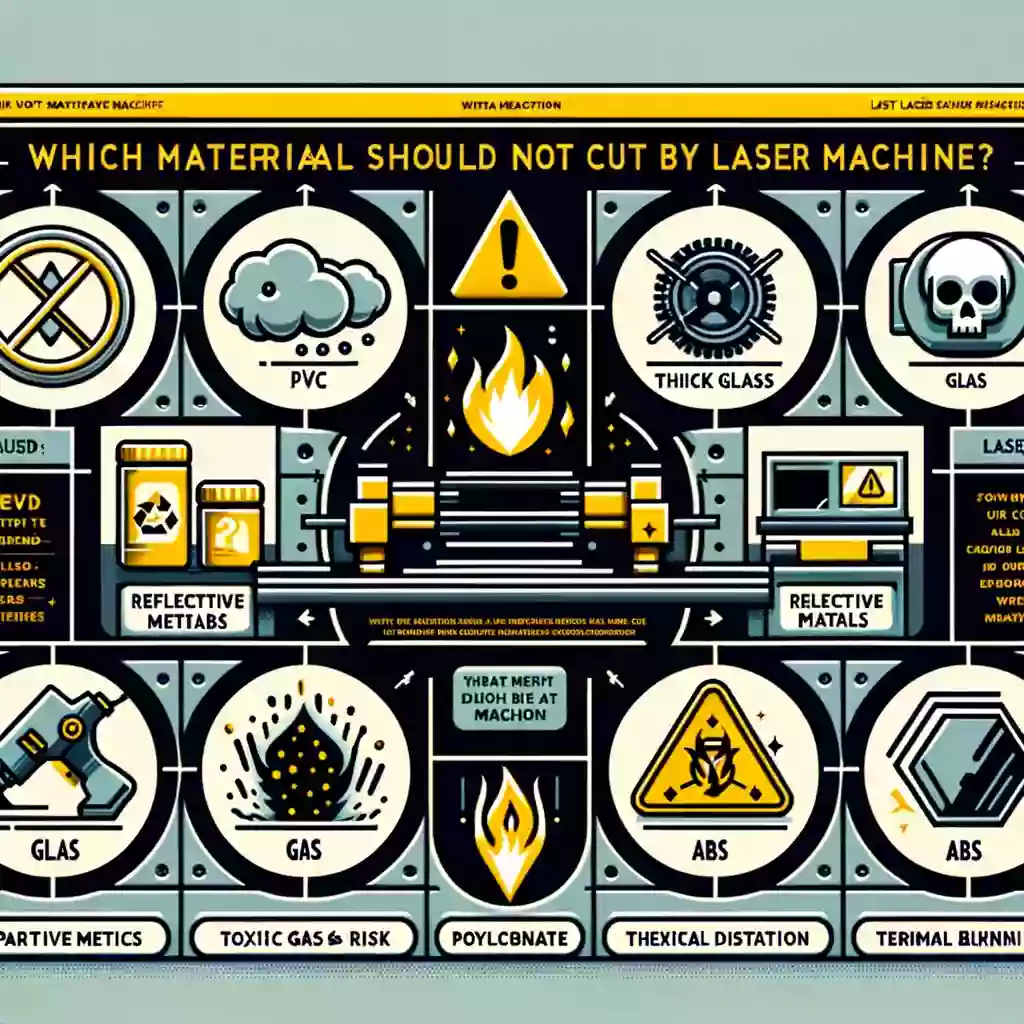
Ⅰ. PVC (polyvinyl chloride)
1.Release Harmful Gases
PVC is a common plastic material widely used to make a variety of products. However, when using laser to cut PVC, it will release hydrogen chloride gas, chloride and other harmful gases.
Be danger to human health
These gases are extremely dangerous to the human respiratory system, and long-term exposure can cause serious health problems.
Corrode laser cutting machine
When these gases are heated, they will produce highly corrosive hydrochloric acid, which will seriously corrode the optical components and metal parts of the equipment as well as the laser cutting machine.
2.Alternative Method:CNC Cutting or Mechanical Sawing
In addition, CNC cutting or mechanical sawing as alternative methods can effectively avoid these problems and ensure safe and environmentally friendly processing. In the advertising industry, PVC materials are commonly used when making large billboards. Using CNC cutting instead of laser cutting can not only avoid the generation of harmful gases, but also ensure smooth edges and improve product quality.
Ⅱ. Thick glass
1.Uneven Cuts or Cracked Glass
Laser cutting works well when working with thin glass, but for thicker glass, laser cutting may not be the best choice. The main problems with thick glass are laser penetration and non-uniformity of heat diffusion. The laser may not penetrate thick glass evenly, resulting in uneven cuts or cracked glass.
2.Alternative Method: Waterjet Cutting
In order to process thick glass, the more common method is waterjet cutting. Waterjet cutting technology uses high-pressure water flow mixed with abrasives to cold cut the glass, which can accurately cut complex shapes without generating thermal stress. This is critical to protecting the integrity of the material.
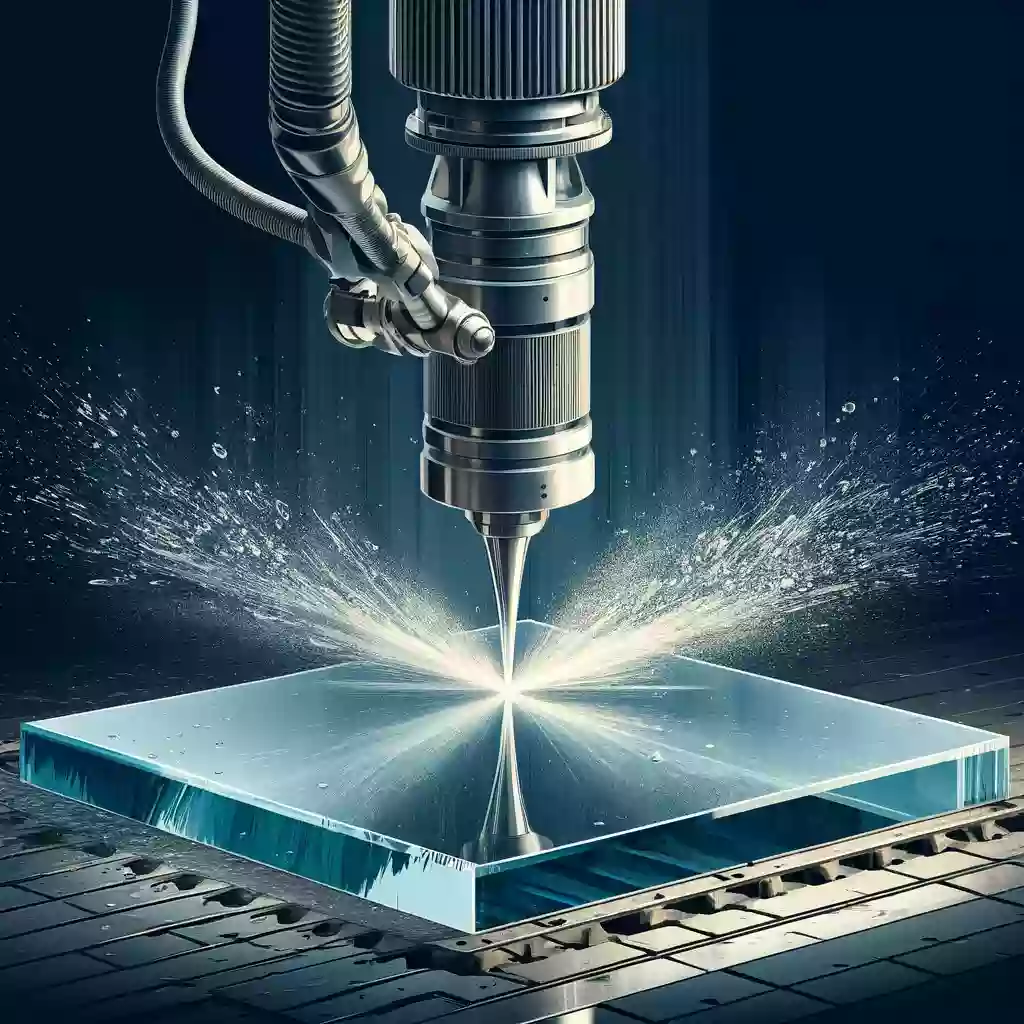
Ⅲ. Metal reflective materials
1.Reflect Laser Cause Damage to Machine and Operators
Highly reflective metals, such as copper and aluminum, are materials that require special attention when laser cutting. The reflective nature of these materials can cause laser light to reflect back into the machine’s light source components, causing serious damage to the laser cutting machine and optical system. Even a small percentage of reflections can cause permanent damage to your equipment.
2.Alternative Method: Plasma Cutting
One alternative is to use plasma cutting. Plasma cutting technology is an effective alternative. It uses ionized gas to cut metal at high temperatures, which causes little damage to the equipment and has fast cutting speed. It is suitable for rapid cutting of thick metal materials.
Ⅳ. ABS plastic
1.Produces Pungent Odor and Smoke
In toy manufacturing, it is often necessary to cut ABS materials to make parts. ABS is a commonly used engineering plastic, but it produces pungent odor and smoke when laser cutting. These emissions can pose a health risk to operators and pollute the work environment.
2.Alternative Method: Using a CNC Machine
Using a CNC machine to process ABS is a safer option. Using CNC machine tools for processing can completely avoid the generation of harmful gases while high-precision and complex shape processing can be achieved
Ⅴ. Polycarbonate
1.Yellowing and Thermal Deformation
In the automotive industry, polycarbonate materials are commonly used to make transparent car parts such as windows and light covers. Polycarbonate is prone to yellowing and thermal deformation during laser cutting. This will affect the appearance quality of the product. In addition, the fumes generated during processing may pose health risks to operators.
2.Alternative Method: Mechanical Cutting and Cold Cutting
Mechanical cutting is a better option that can avoid these problems and ensure the processing quality of the material. In addition, cold cutting technology is an effective way to process polycarbonate, preventing the adverse effects of heat on the material.
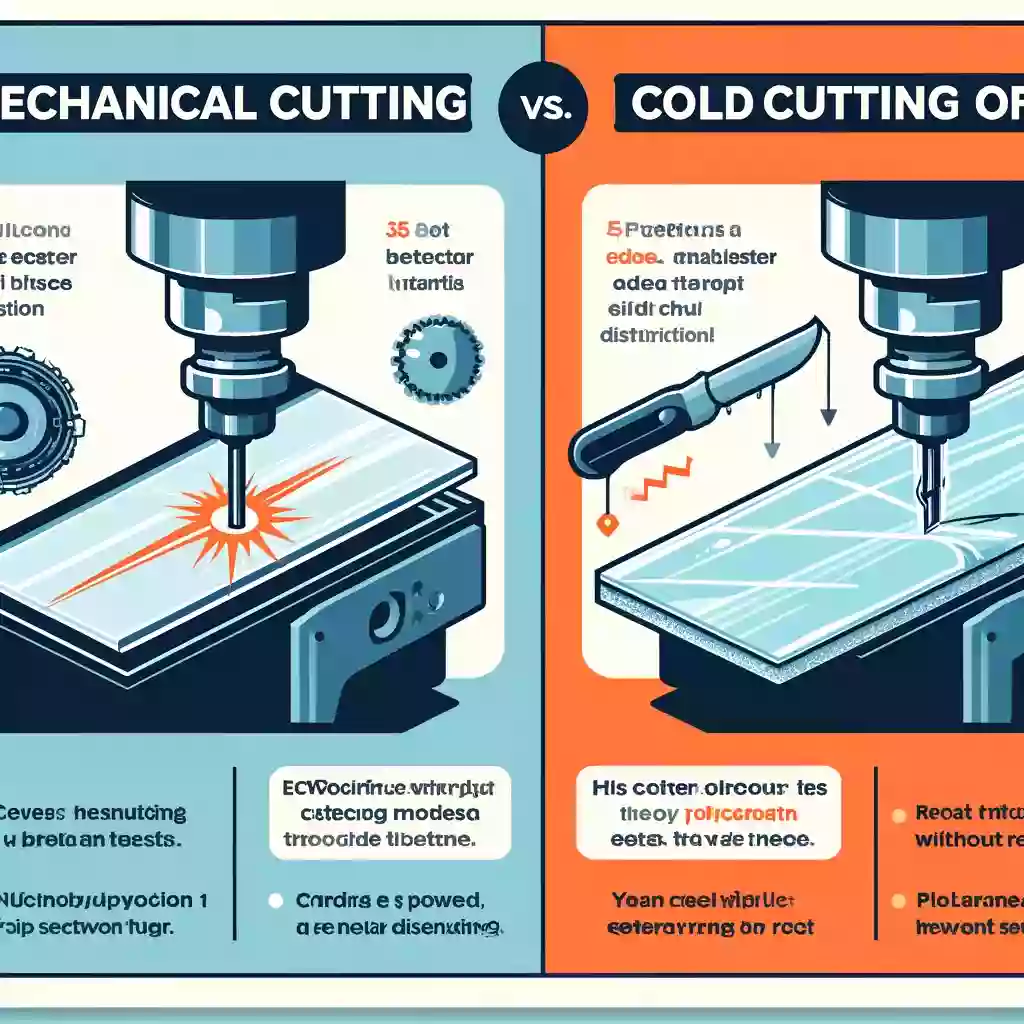
Final Thoughts
Although fiber laser machine is an efficient and precise processing method, it is not suitable for all materials. Choosing the right materials and suitable processing techniques are critical to ensuring product quality and safety, protecting operator health, and long-term equipment use. Before deciding to use laser cutting, it is important to evaluate the material properties and possible risks so that you can make the best production decision.